Rieter is addressing the market requirements for cost optimization in compact spinning with its compacting device COMPACTeasy. This mechanical compacting solution can spin high-quality yarn from all common raw materials at a high productivity rate. Competitive price and minimal maintenance and energy requirements make COMPACTeasy the device of choice for spinning mills in India.
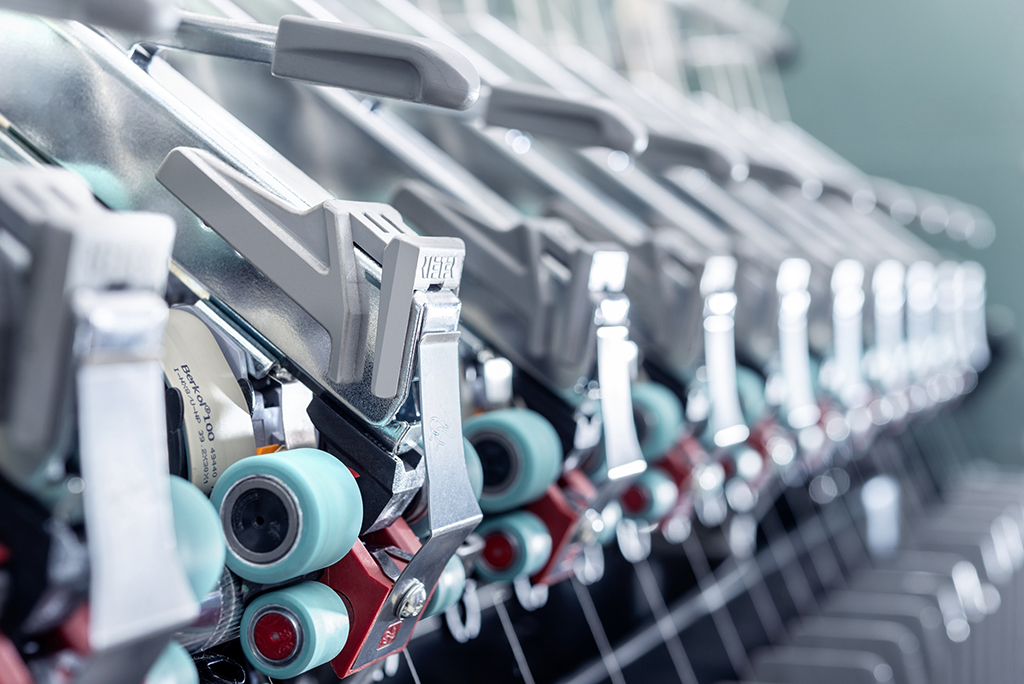
While ring spinning is still the predominant end spinning system in India, there is a notable trend underway in this market toward converting conventional ring spinning machines to compact-spinning machines. Improved yarn properties result in better running behavior in downstream processes and better fabric appearance. Moreover, there is a growing demand from big brands to use compact yarn instead of conventional ring yarn. Compact spinning is appreciated for its excellent yarn quality and high productivity. Saving energy and investment costs are decisive factors for spinning mills today. Other compacting systems require both a high level of initial investment as well as considerable operating costs. By developing the compacting device COMPACTeasy, Rieter’s subsidiary Suessen is addressing this market requirement for optimized costs (Fig. 1).
Covering Most Applications
COMPACTeasy is a mechanical compacting solution for all standard applications. It is attracting customers thanks to its low investment costs. This does not mean compromising on top-notch yarn quality compared to pneumatic compacting systems. COMPACTeasy produces yarns with excellent characteristics from all standard raw materials, such as cotton and man-made fibers, as well as their blends. With a yarn count range from Ne 20 to Ne 80, COMPACTeasy covers most applications.
Constant yarn quality and low maintenance
COMPACTeasy is characterized by precise fiber guiding in the y-channel of the compactor, which results in intensive double compacting (Fig. 2). This process does not require any additional energy.
Compared to other mechanical systems, the compacting channel of COMPACTeasy is much wider, so it is less prone to clogging. In addition to this, the roller does not require grinding thanks to the traverse motion of the compactor. This helps to extend the service life of the components, such as cots or aprons, and significantly reduces maintenance requirements. The traverse motion system enables a consistent yarn quality. This provides a considerable advantage over flipping the front top roller, which is usually required in mechanical systems.
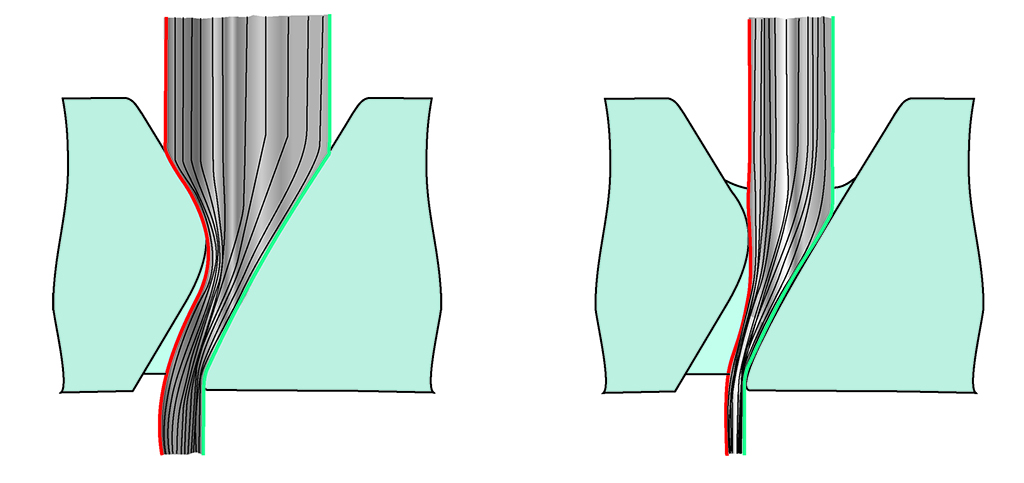
Less Wear and Tear
The device consists of a front top-roller retainer and the smaller COMPACTeasy roller. The compactor features the y-channel and the preceding pin and is located between the two top rollers. The compactor spring uses a low spring force to press the compactor against the bottom roller. This causes considerably less wear and tear on the compactor than magnetically loaded compacting elements.
The yarn quality is determined by both the y-channel of the compactor and the integrated pin. It takes effect precisely in the zone of the drafting system where the fibers have the least guidance. This process reduces yarn hairiness and increases yarn tenacity. It further improves yarn irregularity and yarn imperfections.
Fast Plug-On Plug-Off
COMPACTeasy can be added to the specifications for new ring spinning machines and supplied at the same time. Furthermore, it can easily be retrofitted without additional efforts to existing Rieter ring spinning machines. No additional pneumatic system or gearing reinforcement is required. COMPACTeasy enables production to switch from conventional ring yarn to compact yarn by simply installing or removing the compacting device on a ring spinning machine with fast plug-on plug-off ability.
Overall, COMPACTeasy is a very attractive solution for spinning mills due to low investment costs and no additional energy requirements. The increased yarn tenacity and consistency in quality, as well as the ability to spin a wide range of fibers and yarn counts complete the benefits of this mechanical compacting system.