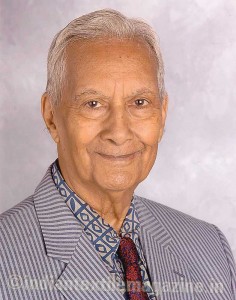
Century Textiles and Industries Ltd., a trend-setter in cotton textiles, also has its remarkable presence in the yarn, denim, viscose filament rayon yarn, tyrecords, caustic soda, sulphuric acid, salt, cement and pulp and paper industries. Incorporated in 1897 as a public limited company, Century Textiles had only one industrial unit, Cotton Textile Mills till 1951. Since then the company has made rapid progress in widely diverse fields. In 2008, the company added to its fold, a vertically-integrated textile plant, Birla Century at Jhagadia, Bharuch in Gujarat.
The company’s 100-per cent cotton yarn unit is situated in Madhya Pradesh, with a capacity of 24,960 spindles. Its denim unit is in Madhya Pradesh, with a capacity of 21 million metres of denim fabric per year. Viscose filament yarn (VFY), tyrecord and chemicals are manufactured at Kalyan (near Mumbai) in Maharashtra. The company has four cement plants at different locations, with a total cement manufacturing capacity of 10 million tonnes per annum.
Century Textiles and Industries has registered net sales of Rs. 6,476 crores in 2013-14 against Rs. 5,863 crores in 2012-13.
In order to cater to overseas and domestic leading brands and to showcase the strength of the company’s R&D by offering more and more innovative designs and products at a faster rate, Birla Century has set up a new facility in a separate research and development centre, for a Pilot Sampling plant. This pilot sampling plant gives more than 300 new fabric yardages of 30 meter each, every month with new colours, designs, weaves, finishes, etc., which is helpful for creating an up market collection range to offer to the niche segment. This helps us in being more innovative while developing new fabrics with various designs, blends, etc., concurrently this invariably increases the potential to go for a high value business with effective but smaller trials.
Additionally, the versatile infrastructure of the centre will reduce the lead time for development to give quicker customer service, which also increases the quality improvement in production trial activities.
Advanced denim fabric processing machine
At Century Denim a new advanced denim fabric processing machine, i.e., desizer-cum-merceriser with dyeing range, has been installed. During processing this eliminates the marble effect in the fabric which gives value addition and is equipped fully with desizing, mercerizing and dyeing facility. On this combo machine all wet finish and mercerized fabric can be dried instead of a stenter machine which reduces drying costs, improves quality, eliminates back staining and gives consistency to the product. Further, desizing improves luster of the denim fabric and the hand feel. It also eliminates batch to batch shade variation and finally after processing, the denim fabric looks flat and clean which is much in demand.
Rayon
Three rayon spinning machines were added to cater to increasing demand of fine denier yarn. The machines were built by using indigenously developed parts and components. In view of a good market demand for fine denier in continuous spun yarn, ten CSY machines were added to increase the total number of machines to 38. With the addition of these machines, about 1.5 tonnes offine denier yarn was added to its capacity every day. The division received Oeko-tex standard 100 Certificate for producing Viscose Filament Yarn which is completely safe for human body and is free from any kind of harmful substances. It also won the Oeko-tex special award for sustainable efforts at Frankfurt, Germany.
Exports
The textile division of the company has made innovative products and exported bed linen with Supima and Egyptian Cotton to the US and Australia, fine count yarn dyed shirting to the UK and Hong Kong, drills for industrial use to Germany, and pocketing cloth and flat finish or cotton lycra denim to Bangladesh, the UK, the US, Peru, Colombia, Kenya and Russia. In case of viscose filament yarn, efforts were made to export larger quantities of dyed yarn to South America and Europe which resulted in better overall export realization compared to that of the domestic market. The overall exports of the company amounted to Rs. 529 crores in 2013-14 as against to Rs. 415 crores the previous year, which was about 8 percent of the net sales.
Demand for viscose filament yarn (VFY) declined after September 2013 leading to a continuous increase in inventories both at the unit and industry levels. Appreciation of the rupee recently against the US dollar has reduced landed cost of material from China thus putting additional pressure on the industry to re-adjust its prices. A demand-supply imbalance coupled with a subdued market for the fabric had also adversely impacted the consumption of VFY.
Consumption of pot spun yarn (PSY) as well as CSY is gradually shifting from coarser denier to super fine denier which invites increased imports from China. Available capacity in the industry to cater to the changing pattern of demand is inadequate and it is expected that imports will continue to dominate despite the levy of an anti-dumping duty.
New pollution control norms proposed to be introduced by the Government will increase the operating cost further. Consumption of Rayon Tyre Yarn, mainly used abroad as reinforcement material in Ultra High Performance (UHP) passenger car tyres has grown both in Europe and Japan and this has helped the unit to increase its capacity utilization to about 80 per cent.