Climate change is undeniably progressing. CO₂ neutral production is being discussed and there are calls to pay even more attention to the recyclability of end products in the textile chain in the future. This has brought textile producers, machine builders, fiber manufacturers and the chemical industry even closer together. Not only manufacturers of classic textiles, but also producers of industrial textiles or textile floor coverings are challenged here.
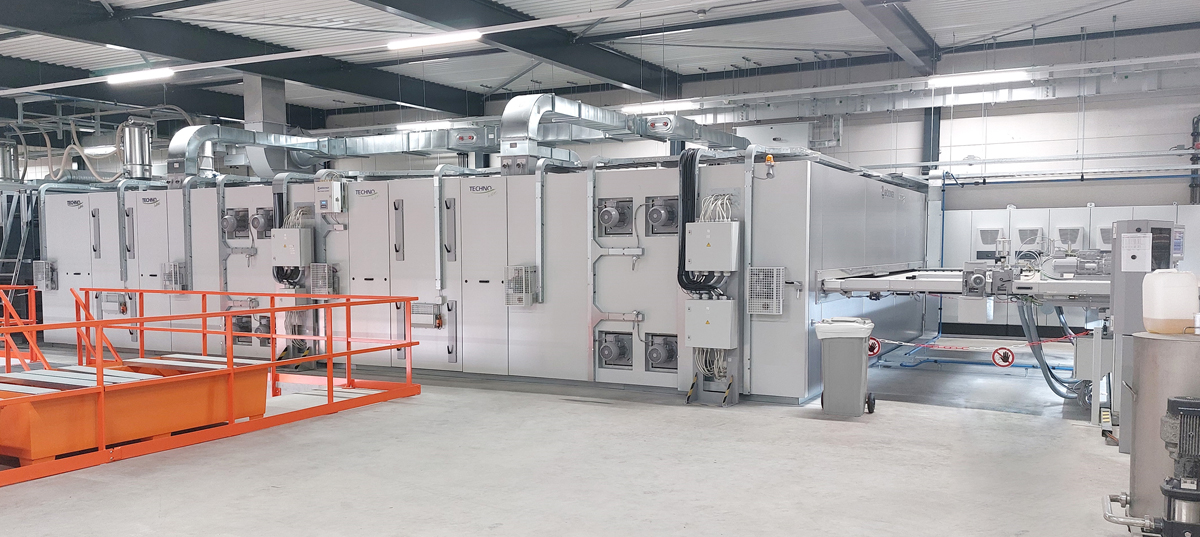
The Dutch floor covering producer INTERCARPET has made a very large investment – driven by the ambitious goal of bringing both a CO₂-neutral produced and recyclable floor covering to the market. But this major goal in terms of environmental standards was not the only focus of the development. The end product should also surpass any conventionally produced carpet in terms of quality, ease of installation, weight, comfort, maintenance and cleaning properties.
INTERCARPET is a major supplier of textile floor coverings in the medium and higher market segments. In two factories in the Netherlands, woven carpets, tufted carpets, knitted qualities and artificial grass coverings are produced for export worldwide. In addition to the typical carpet qualities made of all common man-made fibers, wool qualities of the highest quality are also produced from virgin wool. INTERCARPET has always been a pioneer in terms of reducing the burden on nature and the environment, a fact that has been repeatedly questioned in many audits over the years. Waste management and energy efficiency are not only buzzwords at INTERCARPET.
BRÜCKNER Textile Technologies, a medium-sized, owner-managed engineering company and market leader in the field of textile dry finishing, is proud to have been selected as partner in this project. BRÜCKNER’s delivery includes a stenter with a non-lub ball bearing chain and a DUO-THERM heat treatment oven. The special feature is that the oven is completely electrically heated. With its experience in the field of electric heating BRÜCKNER makes a valuable contribution on the way to a CO₂ neutral future. The oven is operated with green electricity and thus offers for the first time the possibility of a CO₂ neutral production of tufting carpets. All electricity consumers such as fan drives, exhaust air fans or the drives of the fabric transport system are equipped with energy-efficient motors. The horizontal ball bearing chain also ensures lowest drive power due to low rolling friction.
Today BRÜCKNER offers all common heating systems for its thermal treatment and drying lines. This includes direct or indirect gas heating, thermal oil heating, steam heating in low pressure and high pressure version, the described electric heating or also combinations like e.g. steam heating with additional electric heating.

With more than 400 employees BRÜCKNER designs lines for the textile finishing industry, for the production of nonwovens articles or industrial textiles from event tents to advertising banners, automotive textiles and geotextiles for land reinforcement or road construction.
INTERCARPET’s new product portfolio offers even more innovations to come. The new recyclable product and its innovative CO₂-neutral production are in any case an important step towards a green future. This is also sufficient proof that CO₂-neutral production in textile finishing is not just a vision of the future, but that INTERCARPET has already arrived in the future with its new production line and new technology.