Gearing up fast to meet growing local demand
The Ahmedabad-based Bodal Chemicals Ltd. exports about 50 per cent of its overall production and a massive 80 per cent of its dyestuff production to more than 40 countries.
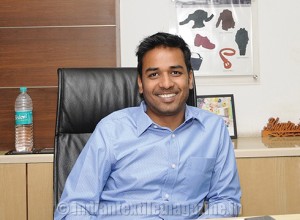
Bodal Chemicals was started in 1990 by its current Chairman, Mr. Suresh Patel. It began as a manufacturer of vinyl sulphone (Para Base), which is a dye intermediate. Within 25 years, it became a vertically integrated company and progressed to production of dyestuff and also raw materials for dyes intermediates.
Mr. Bhavin Patel, a Director at Bodal, started the dyestuff division and is currently in overall charge of the division. He proudly shares with The Textile Magazine that Bodal currently is among the very few vertically integrated dyestuff manufacturing companies across the world.
In 2004, the company started production of dyestuffs for textile, leather and paper industries. In 2006, it went public, and in 2007, it started operations for producing raw materials for dye intermediates like sulphuric acid, beta nepthol, chloro sulphonic acid, oleum, etc.
The company currently operates eight plants in Gujarat – five in Ahmedabad, two in Padra near Baroda, and one in Ankleshwar. The plants together employ around 2,500 people. In 2014-15, Bodal Chemicals sales crossed the Rs. 1,000-crore mark.
The dyestuff division at Bodal has an annual capacity of 17,000 tons, 30,000 tons for intermediates and 190,000 tons for sulphuric acid. The dyestuff division consumes 40 per cent of the dye intermediates produced by Bodal, with the rest sold in the market. Similarly, the dye intermediates division consumes 50 per cent of the basic chemicals produced, with the balance sold in the market.
Bodal Chemicals produces the whole range of textile dyes like bi-functional dyes, printing colours, high-strength and pure dyes, sulphone-based dyes, etc. It can be called a one-stop shop catering to all the needs of fabric processors.
Bodal exports about 50 per cent of its overall production and a massive 80 per cent of its dyestuff production to more than 40 countries. In India, most of the dyestuff business comes through over 40 agents appointed across various Indian textile hubs.
The main export markets of Bodal are Turkey, Bangladesh, Pakistan, South Korea, Brazil, Mexico and a few European countries. It even exports a few dyestuff products to China, although the latter accounts for 80 per cent of the worldwide dyestuff output.
According to Mr. Patel, the company dyes meet all international environmental standards, with the production facilities complying with pollution control standards. The dyestuffs are eco-friendly, and while 80 per cent of products are GOTS-certified, they are also REACH-complaint and meet the Oeko-Tex Standard 100 norms.
In making a comparison with the competitors, Mr. Patel says that, being a vertically-integrated company, Bodal has proved a reliable supplier of dyestuff, cost wise and also quality wise. In the last two years, dyestuff prices became very volatile, going up by as much as 200-300 per cent within just a few months and also falling back again a little later.
In these high volatile conditions, Mr. Patel says it becomes very difficult to honour contracts. However his company could manage the situation. What particularly sets the company apart from its competitors is its capacity to offer dyes at competitive prices even in a critical period of extreme volatility.
The volatility, according to Mr. Patel, happened because of the strict pollution control norms imposed by the Chinese Government which led to its clamping down on industries producing dyestuffs, dye intermediates as well as producers of raw materials for intermediates. It also imposed restrictions on the quantity that any company could produce. Since the Chinese control 80 per cent of worldwide production, volatility is just inevitable.
Alongside offering eco-friendly dyes to the textile industry, Bodal also maintains strict environmental norms at its production plants. When discharging water into the environment, the company maintains COD and colour levels. It has its own biological treatment plant and also an effluent-treatment plant. The water before discharge also goes through Fantone reaction, which ensures that the discharged water is free of chemicals, as also of ‘water white’ colour.
In order to achieve sustainable means of production, currently the company is reusing 30 per cent of the treated water at its in-house ice plant, all of which earlier used to be discharged. In the next six months, Bodal plans to install the RO technology, which will recycle the water which will be reused in its various processes. This will help reuse 70 per cent of the discharged water and save on fresh water.
The year 2014 was a challenging one for the dyes industry which witnessed high volatility, with prices rising and falling by as much as 300 per cent in a period of 8-10 months. This was the toughest period. Mr. Patel reveals that companies across the value chain lost heavily as most had stocked up assuming that prices would escalate further. However, this did not happen. Instead prices again fell back to levels seen before volatility set in. This also led to demand falling by as much as 30 per cent in 2014 as against that seen in 2012 or 2013.
Challenges, according to Mr. Patel, still remain in 2015, but of a different kind. Here he cites worldwide currency fluctuations, political instability in Eastern Europe, and economic instability in Greece, Spain and Portugal as the main cause for concern. He, however, notes that demand for dyes has improved in 2015 as against 2014, but is still 12-15 per cent down from, say, 2012 or 2013.
Mr. Patel claims that the fabrics from textile processors that use their dyes go into designing and producing apparel collections for clothing retailer giants like Macy’s, JC Penney, Tommy Hilfiger, Prada, Zara, Walmart, Nike, etc.
Mr. Patel has high appreciation for the Make-in-India program initiated by the BJP Government as, according to him, the program would help boost the prospects of the manufacturing sector which would in turn create high employment opportunities in India. It would also help India become a global manufacturing hub as has happened in the case of China, but which is now losing its competitiveness because of rising costs.
With China starting to lose its edge and with expectations soaring high under the Make-in-India program, Bodal is gearing up to meet the growing demand. His company is planning expansion of its dyestuff capacity by around 50 per cent in the next two-three years, as it expects the next 10 years to be most favourable for the industry.