BMS showcased the latest version of its Manufacturing Execution Systems (MES) for weaving, knitting, tufting and spinning, all based on the wireless data collection technology. All of these systems include software modules for real-time machine monitoring, production scheduling, fabric inspection, yarn inventory management and traceability. A complete new generation of touch-screen based data collection hardware (data units) as well as a data collection device supporting both Wi-Fi and Bluetooth wireless communication were introduced.
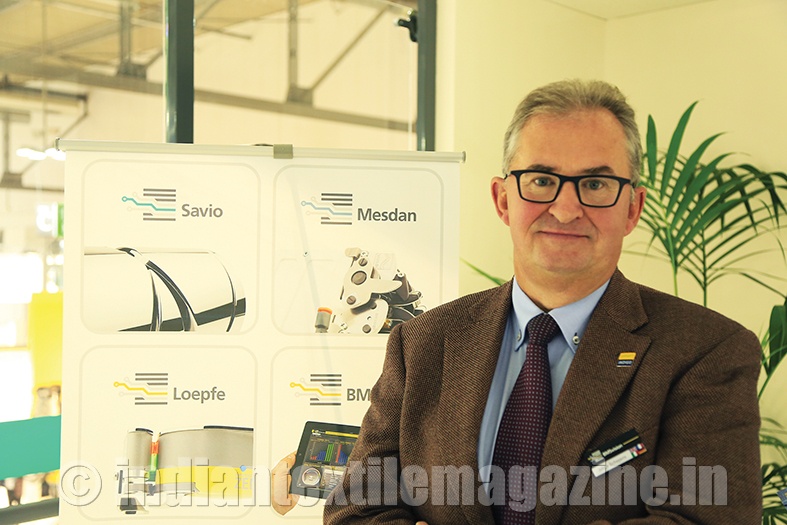
A new version of the report generator now allows combination of real time data and history information in the same reports.
BMS also presented its EnergyMaster system for monitoring the energy consumption in the plant and reporting of the CO2 footprint of the company. The combination of energy consumption values with other MES applications, such as monitoring of spinning, weaving and finishing operations, provides a perfect insight into the relation between energy consumption and production and allows quick identification of energy saving potentials.
For fabric inspection, the Cyclops automatic on loom inspection system with its latest software features supporting inspection of grid fabrics, carbon and Kevlar fabrics and various other types of technical fabrics was exhibited. For grey and finished inspection, a brand new inspection terminal, the QT, in combination with the latest version of the QualiMaster software was presented.
All BMS applications now also support the use of mobile devices for both data entry and reporting. As such, weavers can for example enter declarations or consult information from the server on a tablet or mobile phone. A new module “Management Dashboard” allows the combined presentation of data available in different software modules into one single web-based report. With this tool, the user can create his own dashboard showing all important KPIs at a glance. As such, the manager can have all important information on efficiencies, quality and energy consumption displayed in real time on one single screen, either on PC, tablet or mobile phone. Zooming functions allow him to dig into any further details, if required.
Also on display were the BMS production and quality monitoring sensors and systems for spinning: BarcoProfile for on line quality monitoring on texturizing machines, the OptiTwist real time monitoring system for twist level on twisters and direct cabling machines, and the OptiSpin sensor for spindle per spindle monitoring on ring frames. All these sensors can be connected to the SpinMaster MES system.