The company is well-known for its high quality standards and emphasis on sustainability
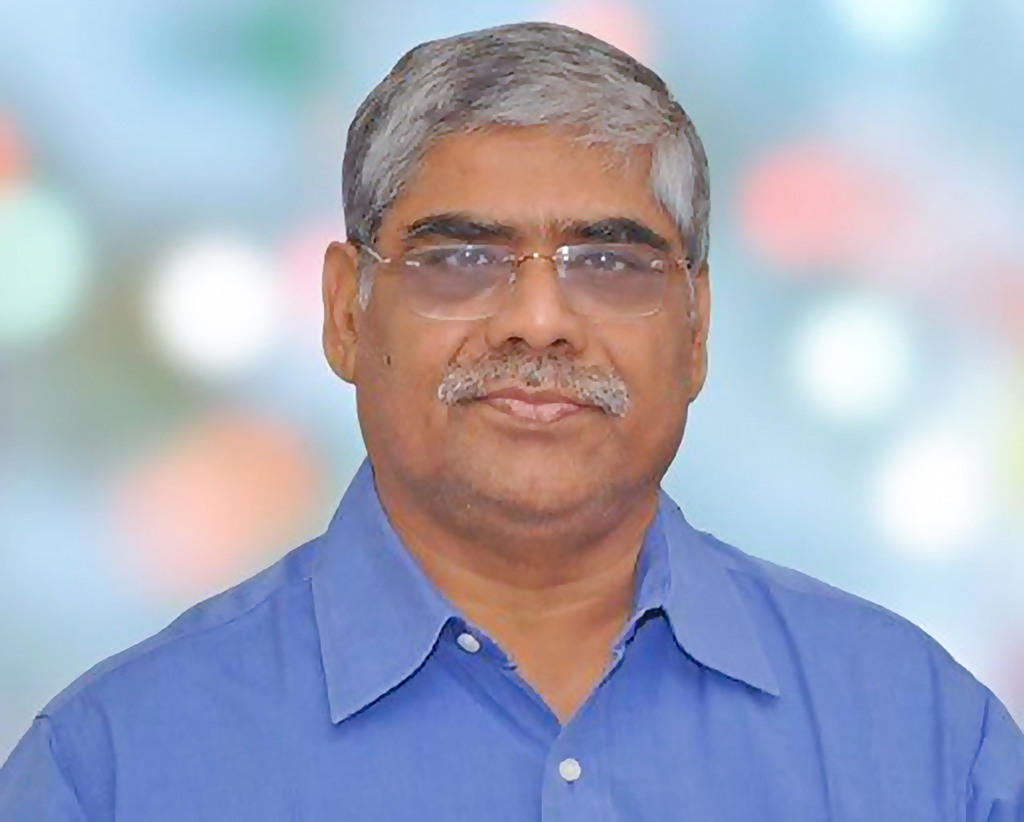
BKS Textiles, a family run business established in 1985, is a vertically integrated manufacturer and exporter of home textiles, institutional linens and woven fabrics. BKS is located in Palladam, near Coimbatore, Tamil Nadu. The company has in-house weaving, processing, and sewing facilities with more than 1,000 employees. Up to 95% of BKS’s production is exports and it works with home textile brands in USA, UK, Europe, Australia, Canada and Japan. The products and solutions offered by the company include bed sheets sets, duvets, pillows, quilts, comforters, blankets, kitchen linens, cushions, table linens and napkins for hotels, ready-to-cut dyed and printed woven fabrics for garments and home textiles.
“We have in-house dobby weaving with production capacity of 30,000 metres per day, narrow width processing facility of 70,000 metres per day and wider width processing facility of 40,000 metres per day. We have 350 sewing machinery capacity to make 5,000 bed sheet sets, 2,000 table cloths, 50,000 napkins and 3,000 blankets per day,” says Director Ms. Sudha Anand while sharing details regarding the manufacturing infrastructure and capacity of BKS.
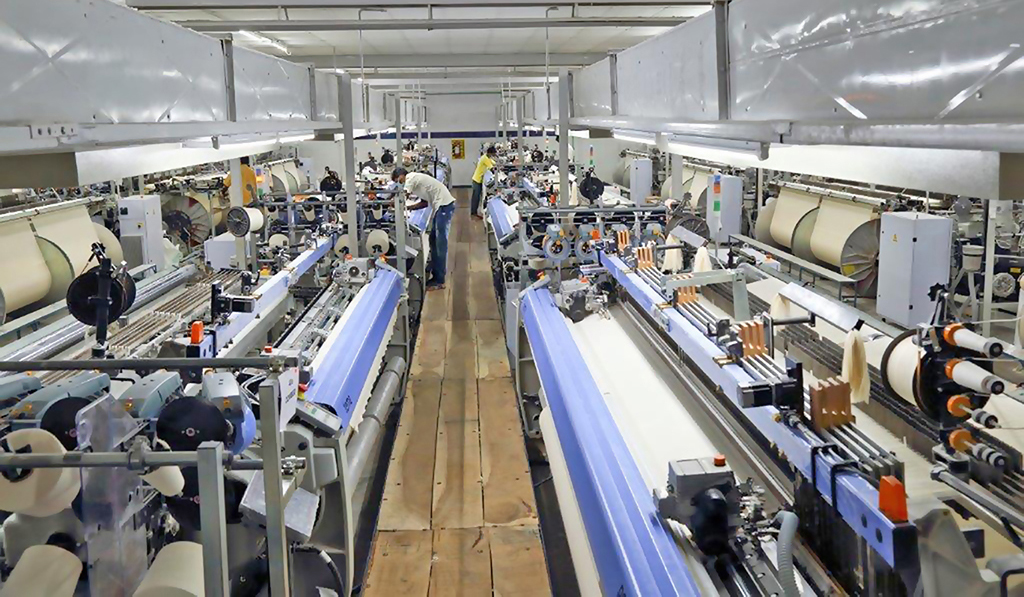
When queried about any recent investments by the company, she replies in the affirmative and adds: “We recently put up a wider width processing plant with production capacity of 40,000 metres per day. The unit is equipped with European machinery and state-of-the-art infrastructure to give consistent high quality to cater to global bed linen brands in cotton, polycotton, Tencel, linen etc. All our processing facilities are equipped with effluent treatment plants that ensure recycling and reuse of 95% of effluent water and zero liquid discharge.”
“At BKS we give great emphasis to sustainability and we are well known as a supplier of sustainable home textiles and woven fabrics. We follow the tenets of ‘sustainability, responsible manufacturing’ through our policies, processes and certifications like GOTS, Fair Trade, SA8000, Oeko Tex, Step by Oekotex, GRS , BCI and SCAN besides ISO 9001 for quality management, ISO 14001 for environmental management and OHSAS for occupational health & safety,” Ms. Anand elaborates on the company’s sustainability initiatives.
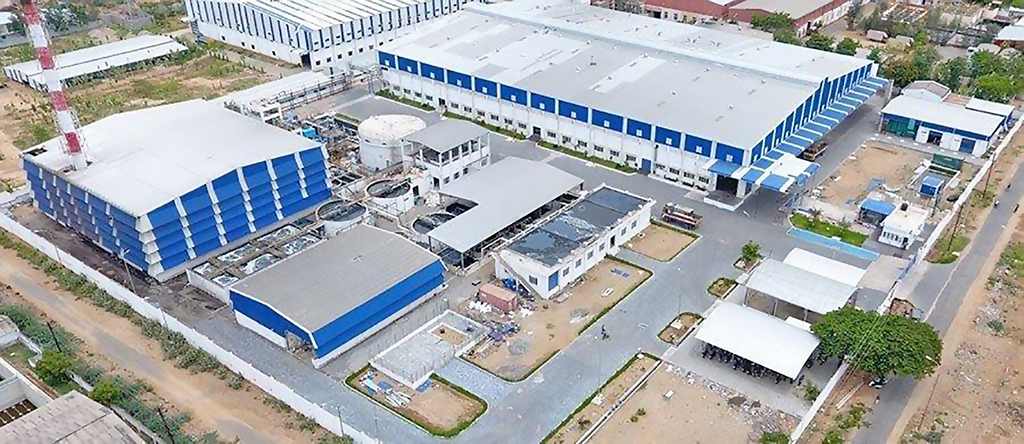
Sustainability Initiatives
Listing out BKS’ recent initiatives towards sustainable manufacturing, she remarks: “We got Step by Oeko Tex certified recently. Our 1,00,000 sq. feet sewing unit is a LEED certified green building and 40% of power requirement is fulfilled through our own windmills.” Going into details regarding the company’s share of domestic business and exports and its key customers in India and overseas, Ms. Anand reveals: “Around 5% of our business is from the domestic market. We do white labelling and sell bed and bath products in our brand name ‘Swaas’ in the Indian market through online marketplaces like Amazon, Flipkart and our own e-commerce store www.swaaslife.com. We see a strong surge in demand in domestic home textiles market after the pandemic and we expect good growth in consumption in Indian market in forthcoming years. Globally, we are supplying to renowned home brands in USA, UK and Australia.”
Highlighting the competitive edge that the company has, she points out that BKS is well-known for its high quality standards and emphasis on sustainability. “Besides high quality, competitive price, state-of-the-art infrastructure, what sets us apart is our values and ethos such as sustainability initiatives, responsible manufacturing and women empowerment,” she explains. Ms Anand further mentions that the company’s sales turnover is USD 25 million and that it has been growing 20% year-on-year for the last five years. With respect to the number of employees working in BKS she says: “We have 1,000+ employees working with us, out of which 65% are women. We are constantly striving to increase the strength of women employees in our company.”
Automation and Growth
The company is also focussed on adopting automation in its manufacturing process. “At BKS we have recently invested in SAP ERP and all the production processes, inventory, plant maintenance are monitored and controlled through SAP. We have online loom monitoring software to capture live productivity and quality in weaving. We have installed fabric inspection software for online quality and productivity monitoring. We are planning to gradually increase automation in all possible areas in the shop floor,” she informs.
The company has ambitious growth plans lined up for the future. Throwing light on them, Ms. Anand says: “With the expansion into wider width processing unit we are now stronger in the bed linen product category. We have all the infrastructure and base to grow as a strong player from India in the home textiles category (bedding, cushions, table and kitchen linens) and we are very optimistic that our sales turnover would increase to USD 75 million by 2025.”
—
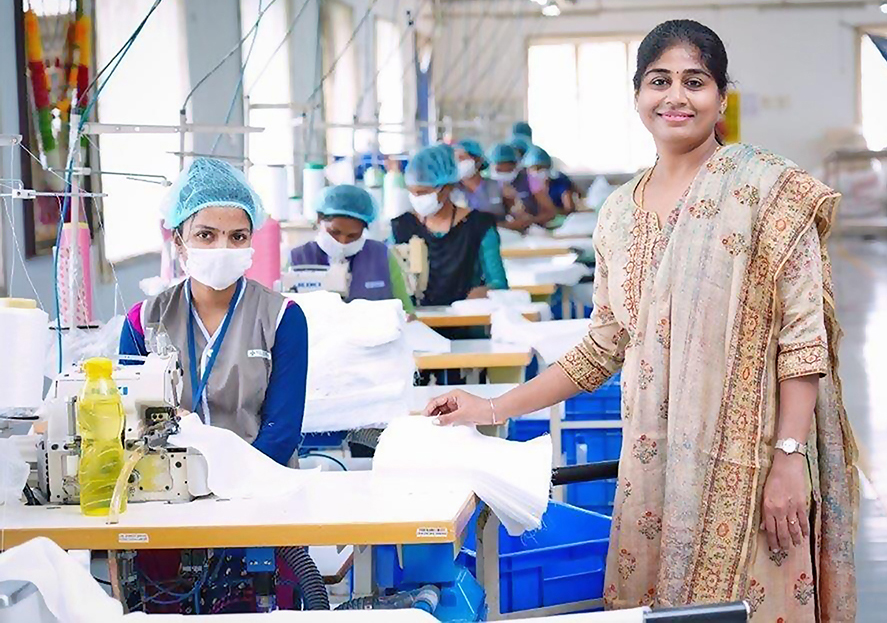
“We have in-house dobby weaving with production capacity of 30,000 metres per day, narrow width processing facility of 70,000 metres per day and wider width processing facility of 40,000 metres per day. We have 350 sewing machinery capacity to make 5,000 bed sheet sets, 2,000 table cloths, 50,000 napkins and 3,000 blankets per day.
– Sudha Anand, Director