Supplying best-quality flatbed screen printing machines has always been the hallmark of Ahmedabad-based Screenotex Engineers. Providing insights into how these high benchmarks are attained and retained is Managing Director Hemant Patel
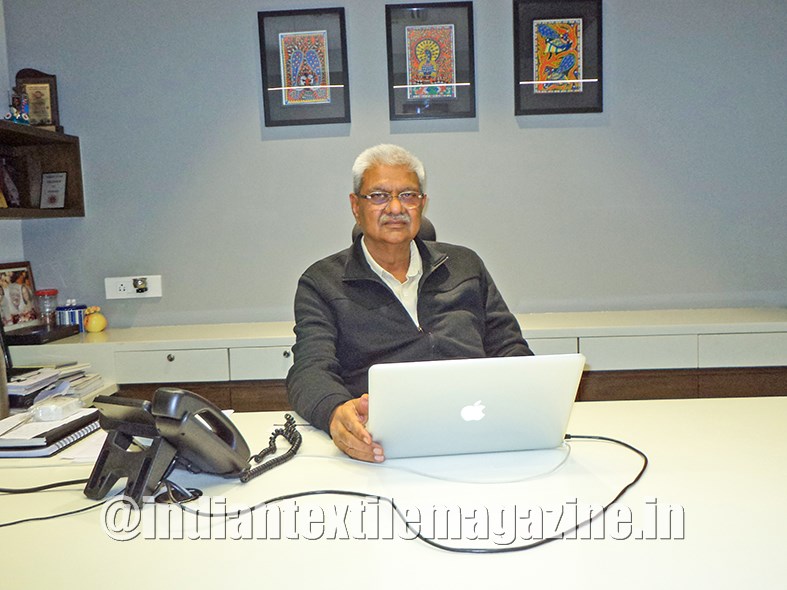
Manufacturing and supplying best-quality textile flatbed screen printing machines has been the hallmark of Screenotex Engineers (P) Ltd. since inception in 1993. Apart from using high-quality inputs, the company also has a self-driven quality control and assurance department, where each and every spare or accessory needed to manufacture the printing machine is tested against set parameters. Apart from such rigorous quality control, Screenotex Engineers sources servo gearboxes from world-renowned companies, which can run at up to 7,000 rpm of input, while locally produced gearboxes can run only up to 1,500 rpm of input.
And that explains why Screenotex Engineers commands such reputation. “We also do a sandblast process on each and every metal part before painting. This is done to remove all the impurities that would have stuck to the metal during fabrication like dirt, oil, etc. This sandblasting process ensures that there is no corrosion to the metal part in the future. This also helps increase the bonding of paint with metal,” says Hemant Patel, Managing Director, Screenotex Engineers. The company also sources electrical and electronic panel boxes from Rittal, Germany, which has a plant in India. These panel boxes are heavy-duty and have a totally dust and moisture-free environment. According to Patel, the life of an electrical or electronic part is reduced when it comes in contact with either dust or moisture.
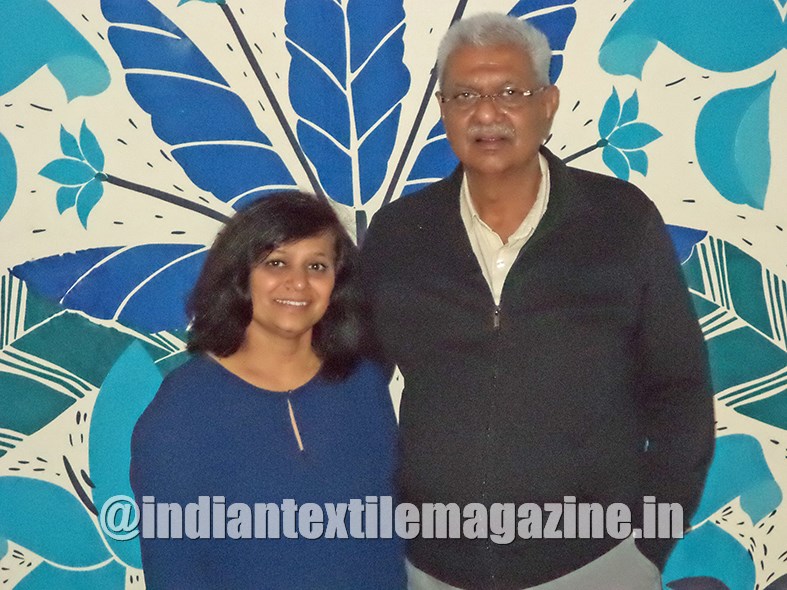
Focus on Quality
“From day one, we have focused on providing the highest reliable quality of machines. We are charging 15-20% more for our machines as against our competitors because all our initiatives go towards making our machines accurate, rugged and sturdy, as when a fabric is not printed accurately, that particular fabric length is sold at lower prices. So, despite our higher price, discerning buyers still prefer to buy our machines,” Patel informs. His biggest satisfaction comes from the repeat orders they get from their long-time buyers like Pratibha Group in Surat which has bought 18 machines till date, Gogad Group in Pali which has purchased 28 machines or Jayshri Group in Jetpur which has 17 machines.
A Fulfilling Journey
Four years back, Screenotex Engineers shifted to a spanking new and fully SAP-enabled facility which is located on the outskirts of Ahmedabad. The new workshop has a built up area of 55,000 sq. feet and office and warehouse space of 18,000 sq. feet along with a 5,000 sq. meters landscaped garden. As of now, the company manufactures around 64-72 machines per year. They also have a dedicated design and research and development department staffed with nine employees.
Moving with the Times
In earlier times, the company used to manufacture semi-automatic flatbed screen printing machines. These machines used to need a lot of labour to operate. Things have changed now considering that labour shortage and higher wages have started pinching the Indian textile industry. This is what prompted Screenotex Engineers to develop and supply fully automated machines. The earlier generation of machines used to work on single-drive technology with many mechanical parts, which was replaced with variable frequency drive (VFD) technology, leading to reduction in mechanical parts and later on to servo-driven machines.
“In the earlier variant of semi-automatic machines, for each colour that was printed, a similar number of labour inputs were required. But in the fully automatic machines, there is no need for this kind of labour, which has led to huge savings on wages. Additionally, the automatic machines also offer far better print registration, sharpness and accuracy and has therefore forced those using earlier technologies to graduate and replace them with automated technologies,” Patel elaborates.
The company offers three models of flatbed screen printing machines. The first is ‘Unique’, which is an entry-level machine. The next is ‘Altima’, which was mainly designed to print wider width fabrics of more than 72 inches. The third is ‘Optima’, a high-end model which can also print knit fabrics. Currently, the Altima accounts for 80-90% of sales, followed by the other two models.“ Rotary or digital printing technologies have never been a competition for us as our buyers are those who print mass volume products like sarees and dress materials. The ‘pallu’ of a saree or a ‘dupatta’ can be printed only on flatbed screen printing machines and not rotary printing machines,” Patel informs.
Sales and Service
As of date, the company has sold 1,500 machines in India and other countries. But a majority of sales are generated from the domestic market as the company exports only to a limited number of countries like Bangladesh, where they have sold around 80-90 machines or Africa, where they have sold around 12-15 machines, while in Indonesia it is around 3-4 machines. “For providing after-sales service, we have two service engineers in Surat and three in Rajasthan and also offer it through remote access to PLC-based machines from our plant. But ever since we started supplying automated technologies, service calls have declined to a great extent. We were attending more service calls 10 years back on a smaller installed base as against today, where our installed base is higher,” Patel states.
Future Roadmap
Patel avers that the textile market has become uncertain and with the cost of maintaining the new facility, it has become imperative for them to explore manufacturing other textile technologies. As such, they are foraying into manufacture of stenters, which will be launched within the next 3-4 months. The stenter has been developed by their in-house research and development team and will have the latest features, but at the same time, will need less maintenance and will be available at an economical cost.