Short filter service lives and labor-intensive cleaning are no longer an issue
Large-area filtration faces the stigma of high costs, maintenance efforts, and time-consuming changeover and cleaning activities. However, good filtration is unavoidable with increasing rPET pro-portions. So, BB Engineering has addressed these issues with its decades of experience in extrusion and filtration. The new COBRA filter combines continuous and automated large-area filtration with integrated intermediate filter cleaning – setting a new standard in efficiency, ease of use and resource saving, and finally meeting the demanding requirements of recycling processes.
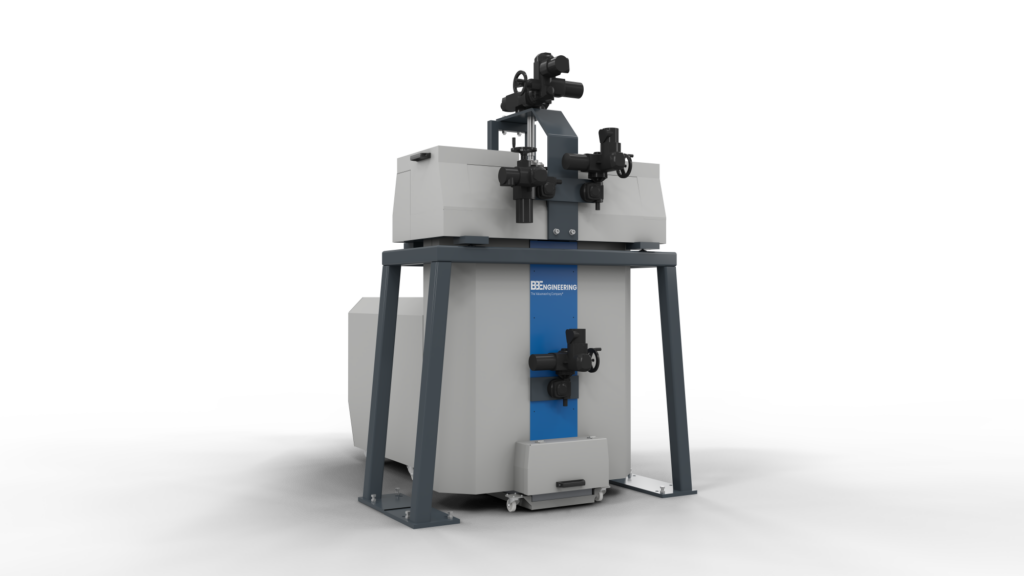
Large-area fine filtration made for recycling
Recyclers are currently dealing with a dilemma when it comes to filtration. Increasing recycling quotas coupled with insufficient availability mean that lower input qualities are also being considered for recycling, resulting in more challenging contaminants. At the same time, higher-quality applications are being targeted, which further intensifies the requirement for fine filtration. There are systems for large quantities of contaminants, but they do not filter as finely as a candle filter. There are also candle filters that provide excellent filtration but cannot cope with high levels of contamination.
The new COBRA filter can do both. It was specially developed for demanding filtration tasks with high levels of contamination, particularly in PET recycling. Multitasking is the keyword. COBRA unites large-area fine filtration with simultaneous, fast and effortless cleaning, and is therefore able to handle higher contamination rates, which common candle filters would fail on. However, this all-rounder can also be used for other applications, e.g. in synthetic fiber spinning
Continuity and process stability thanks to automation As a continuous filter, the COBRA filter has two filter inserts, one of which is always active in production mode and the other either in stand-by mode or in intermediate cleaning. The automated switchover ensures a smooth changeover between the inserts.
The status of the filter inserts is constantly checked by the system and, if necessary, the COBRA filter automatically initiates the cleaning and changeover process. All the operator has to do is confirm this on the user interface – no further manual intervention is required. The process thus continues to run stably and safely without interruption. Operator-related deviations in the switching process, operating errors or delays, all of which could affect the process, cannot occur.
Effortless inline cleaning – effective and safe The highlight of the COBRA filter is the integration of BBE’s White Filter Cleaning technology (WFC). This process enables absolutely chemical-free and environmentally friendly intermediate cleaning of the filter inserts using hot steam alone and extends the filter’s service life many times over. BBE has already had WFC in its product portfolio as a stand-alone solution for several years. Now, for the first time, the cleaning system is integrated directly into a
filter, bringing additional advantages, like cleaning speed and wear-reduction. Production and cleaning becomes an alternating interaction. Only after multiple operating/cleaning cycles (the exact number depends on product and degree of soiling) is it necessary to completely remove the filter insert for a service check and full cleaning. The WFC cleaning process only takes around 10 hours, whereas conventional cleaning takes several days. Filtration and cleaning form a self-contained, automated system that guarantees process and operating safety in equal measure: The operator does not have to handle melt or chemicals.
Development goals: Simplified handling, economic efficiency
BB Engineering pursued clear objectives when developing the COBRA filter: in addition to adapting the system to the growing challenges arising from increasing levels of contamination in recycling, BBE focused on simplifying filter changes and cleaning processes through automation as well as significant savings in operating costs.
And that has been successful. Comparing the COBRA filter with other fine filters with a throughput of 2000 kg/h reveals a saving of 40% in pure operating costs. This saving results from various
aspects. One significant part of the savings comes from the reduction of melt loss through backflush-cycles. Another key point is the continuous operation with significantly longer service life thanks to the integrated cleaning with steam. This is linked to reduced use of spare parts and consumables due to the gentle treatment, conversion costs and a lower energy requirement, as no heating and cooling phases and generally lower cleaning temperatures are required. Costs of chemicals are completely eliminated. Automation reduces personnel costs due to the low operating effort and training requirements. In terms of operation, the COBRA filter is also very safe – the closed system of filtration and cleaning without chemicals eliminates many of the risks associated with conventional filters and cleaning methods, such as the risk of injury and fire. The cost savings are even more far-reaching if you extend the
consideration to the downstream processes. The outstanding cleaning performance of COBRA saves a great deal of effort, interruptions and further processing. The new COBRA filter will be presented to the public for the first time at the PRSE in Amsterdam at the beginning of April.
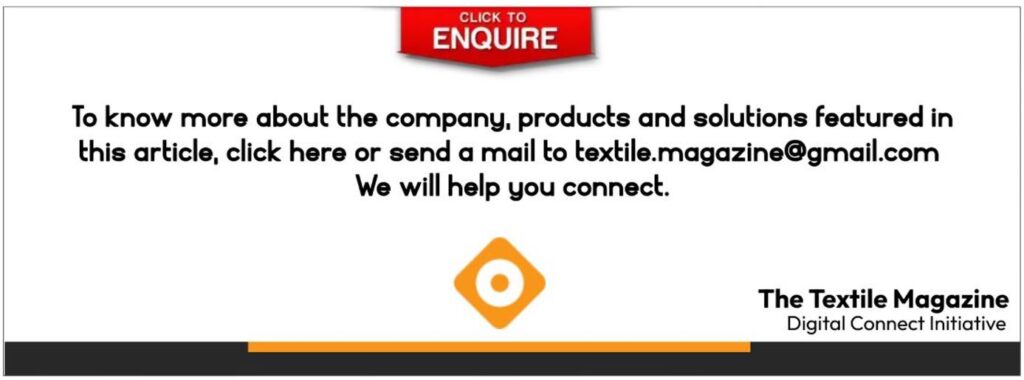