Offers manufacturing solutions for the entire textile value chain
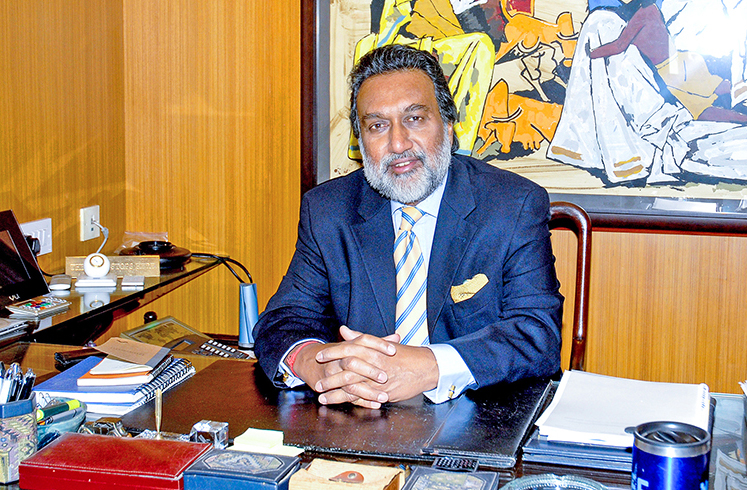
In this exclusive interview, Batliboi Ltd.’s Chairman, Nirmal Bhogilal and CEO-Textile Machinery Group, Abhay Sidham offer insights into the working of the company’s various divisions, in particular the textile machinery segment, and outline the products and technologies offered by its principals along with how sustainable manufacturing is at the core of all its operations
Could you introduce the Batliboi Group and its various units?
Batliboi, founded in 1892, has grown to a position of leadership among engineering companies. The company’s beliefs and values have been the cornerstones on which it has built a durable edifice. It has spearheaded a technological change in all the activities that it is engaged in today: manufacturing, engineering, contracting and marketing. At plants located at Surat in India and Peterborough in Canada, Batliboi manufactures sophisticated machinery. At its Surat plant Batliboi manufactures machine tools, air engineering equipment and industrial fans. The range includes equipment designed and fabricated indigenously as well as from earlier collaborations with some of the world’s leading engineering companies.
Our operations are as detailed below:
• Machine Tools: We manufacture a wide range of products at our Surat facility and the facilities of its 100% subsidiary in Canada, Quickmill Inc. The agency division sources leading brands of machine tools from around the world for sales in the Indian market.
• Air Engineering: We manufacture complete systems for humidification, ventilation and air-conditioning including filtration and waste collection.
• Textile Machinery: We source and supply the latest generation of textile machinery and accessories from leading domestic and international companies in the areas of spinning, knitting, weaving and processing, including waste and effluent treatment.
Within the Batliboi Group, which are the divisions focussed on the textile industry?
Batliboi’s textile machinery group offers the latest generation of textile machinery from leading domestic and international companies. The textile machinery division serves the spinning, knitting, processing, printing and technical textile industry. Batliboi supplies the latest generation of equipment from companies who are world leaders in their respective fields. The company also supplies accessories, consumables and speciality lubricants from renowned companies. Batliboi’s air engineering group is among the foremost players in the Indian textile engineering industry. It is a well-known supplier for a wide range of world-class equipment and a leader in textile air engineering system.
A long association with the textile industry, reliable and high technology equipment and an extensive sales and service network are the hallmarks of Batliboi’s presence in this industry – attributes which few other companies can boast of. Today, we manufacture the entire range of air engineering equipment which includes high-efficiency fans, air washer systems, chiller packages, rotary drum filter, rotary water filter, fibre recovery and condensing systems and other auxiliary equipment. The precise control of environmental conditions in the production facilities are ensured by sophisticated automatic controls.
India ITME is Asia’s largest textile manufacturing show. How important is it for your company? Can you summarise the products and solutions that would be exhibited by you and your principals at the show?
India ITME is the most important trade fair for us, especially given the fact that it is taking place after an interval of six years. Batliboi will showcase sustainable manufacturing technologies at its two stalls with a total area of 426 sq. metres. These are at Spinning Hall 11, Stall H11B17 and H11B19 and Processing Hall 7, Stall H7N7P6. Batliboi is going to participate along with its Principals Mayer and Cie, Ferraro, Mario Crosta, Loris Bellini, Pentek, Eliar, Europrogetti, Ichinose, Fimat, Dettin, Pozzi and Intex at Processing Hall 7 and at Spinning Hall 11 we will have the exhibits of Batliboi’s textile air engineering division and Loptex and Saurer BD’s semiautomatic rotor spinning machines. The participating Principals will showcase manufacturing solutions for reduction of energy consumption, reduction of water, chemical consumption, water recovery and automation.
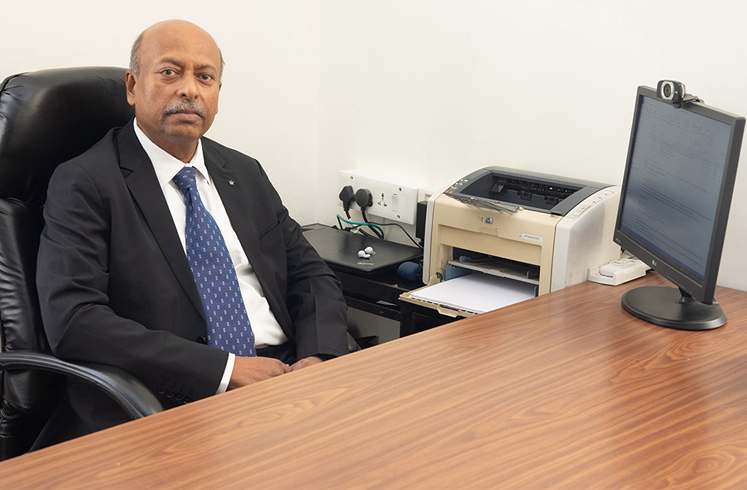
Keeping with the current trend Mayer and Cie will display OVJA 2.4 E electronic jacquard machine for knitted mattress ticking fabric in 38 inch, gauge E20 in an industrial frame. The machine is targeted for the manufacturing of mattress cover fabrics. In the segment of premium mattress ticking, Eliar will display fully automatic dyes dispensing system, controllers, sensors, etc. The main focus will be sustainability and automation in textile manufacturing. We will showcase sustainable manufacturing processes with recycled raw material. Saurer BD’s rotor spinning machines with recycled raw material processing solutions will showcase how the spinning process is the most important part of the material recycling production chain.
Its rotor spinning machines are well-accepted and established as optimised for recycling. Further, for the knitting process, Mayer and Cie is a very well-known brand and it will showcase its sustainable Relanit technology with its eminent advantages for OE and courser yarn knitting capability. This technology reduces friction and tension of the yarn as it works with fewer deflection points than a conventional knitting machine. This is an ideal solution for knitting recycled colour OE yarn at higher production speed with optimum quality and reduced wastage. Relanit technology also contributes to carbon reduction by reducing energy consumption for every kilogram of fabric produced.
Despite global and domestic challenges, the Indian textile industry has been witnessing steady growth in the last couple of years and looks to benefit from the changing global geo-political scenario. What is your assessment of growth in the industry and your expectations about the future growth of the textile industry in India?
We believe that for India the time is now. India is one of the faster growing textile consumption markets, expecting a CAGR of 8% to reach over USD 100 billion by 2026. All the three end-use segments—apparel, home textiles and technical textiles—are expected to see healthy growth thanks to the rising penetration of products driven by increased purchasing power. This is a good sign for India’s textile producers as the growing domestic market should provide an ample boost to production prospects. Meanwhile, the focus on automation, digitisation and sustainability are the other factors that are lending an extra edge to the Indian textile manufacturers to enable them to complete in the foreign textile markets.
Buoyed by a huge spurt in demand in the domestic as well as export markets during the last couple of years, the Indian textile industry is poised for unprecedented growth almost in all its segments. Supported by schemes announced by the government to give a further boost, all leading groups in this industry have initiated massive expansion plans. As per IMF data, the GDP growth of India is expected to be over 7%, which is much higher than many traditional textile producing countries. According to the opinion of leading industry experts, the period of 2022-2025 will be a golden era for textiles in India. To exploit this positive sentiment, India ITME will be a fruitful event.
The government has announced the PLI scheme, PM Mitra and many more to further boost textile manufacturing. The textile ministry has set an ambitious target of achieving USD 250 billion by 2025 for this industry. To achieve this, what is the kind of investment that would be required for new projects, plant and machinery?
To achieve this monumental growth targets in exports supported by robust domestic consumption, the consequent jump in production will have to be driven by new investments. As per the forecast, India might be looking for fresh manufacturing investments of USD 20-25 billion in the immediate term. By 2025, the textile sector in India is anticipated to attract investments totalling US$ 120 billion. The Indian textile industry will have to invest in the latest sustainable technology, automation and digitisation to facilitate competitive costs and sustained quality at optimum production efficiency. Forecasting India’s potential for growth in exports, India should strive for 8-9% CAGR in exports now onwards. Minister of Textiles Mr. Piyush Goyal has set an even higher goal of reaching textile industry collectively USD 250 billion by next five to six years. Textile industry should aspire to achieve the same through sustainable manufacturing.
How is Batliboi Group planning to leverage on its decades of experience and close relationship with customers in taking advantage of the emerging growth opportunity? In your discussion with your principals, how do they view the Indian market and its potential?
With Batliboi Group’s 130 years of legacy and goodwill with its pan-India sales and service infrastructure and most importantly solution-oriented ‘customer first’ policy, we and our Principals are confident about cashing in on the upcoming opportunities. Our Principals are very well-versed about India’s growth potential in terms of growth in production volumes and related technological investments. We have aligned and optimised our products and services to serve customers’ requirements. Batliboi being a fibre-to-fashion solution provider, we are in contact with the entire textile value chain in the Indian market with its massive growth potential. India is definitely a key market for our principals.
In your opinion, which are the segments within the industry which are expected to show promising growth in the coming year, as for example, manmade fibres, apparels, technical textiles, home textiles, etc.? How is your company positioned to cater to the requirements of customers?
We expect growth will be related to MMF and MMCF products. The knits segment, especially active wear, is expected to grow faster. Batliboi with its Principals is all set to provide manufacturing solutions from spinning, knitting to finishing. We offer technologies, customer consulting, turnkey projects, etc. Building on India’s current home textiles’ strength to become a global powerhouse in home textiles will require more eco-friendly sustainable technologies and in this regard our partners such as Pentek, Mario Crosta, Loris Bellini, Fimat, Ichinose, Ferraro and Europrogetti all are very well-positioned to offer sustainable technologies and automation to optimise resources to reduce water, chemical and energy consumption. As far as technical textiles are concerned, this will be the fastest growing segment for which we offer technologies, customer consulting and project support from Mayer and Cie and Mageba for various applications, including medical technology and geo technology. The expected growth is over 10% CAGR in this segment.

Given that the textile machinery segment is highly competitive with solutions available at every price point, why should a customer look to work with Batliboi Group? What are the distinct advantages you offer vis-à-vis the competition?
Batliboi’s textile machinery division, since its inception, has always endeavoured to provide world-class service to its customers. In any project – small or big – technological support is of paramount importance. This is where our textile machinery division scores over others. Backed by technically qualified and trained engineers, Batliboi sets benchmarks for the industry when it comes to service support.
Globally there is an increasing focus on sustainable textile manufacturing. Global brands and retailers are setting sustainability goals specifically for their supply chain. In that connection, how is Batliboi Group supporting its customers in their sustainability mission and targets?
The deteriorating global environment has put the theme of sustainability at centre-stage in every industry, including textiles. As per recent statistics, the global textile industry emits 1.2 billion tonnes of CO2 equivalent each year, close to the level of emissions from the automobile industry. Batliboi is offering sustainable manufacturing technologies and solutions right from spinning to finishing and garment washing. To make the spinning manufacturing process sustainable with recycled raw material, Saurer BD rotor spinning is a proven technology and its rotor spinning machines are well-accepted and established as recycling-optimised spinning machines.
We are helping customers further in the knitting process as well and Mayer and Cie is well-known in this regard for its Relanit technology with its advantages for OE and courser yarn knitting capability. Relative knitting technology reduces friction and tension of the yarn as it works with fewer deflection points than a conventional knitting machine. It is thus an ideal solution for knitting recycled colour OE yarn at higher production speed with optimum quality and reduced wastages. Relanit technology also contributes to carbon reduction by reducing energy consumption for every kilogram of fabric produced. For wet processing and finishing all our Principals offer technologies and knowhow for reduction of energy consumption, reduction of water, chemical consumption, water recovery, heat recovery, effluent treatment plants and automation.
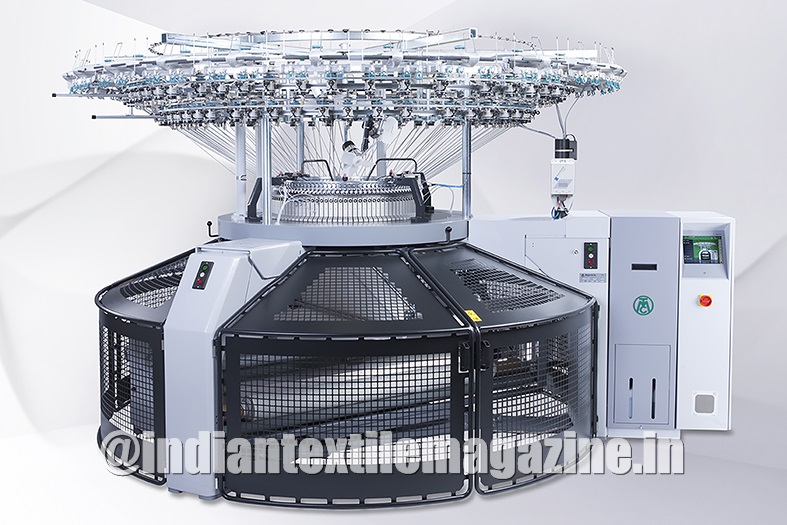
We believe that the textile value chain will have to follow the path of circular economy, which means higher usage of recycled materials. In that respect, India could be a global leader in sustainable textile manufacturing. Sustainable textile manufacturing is not an option anymore. It is the only way to manufacture. Noting how the company’s products and technologies are helping its customers in achieving their sustainability goals, Loris Bellini has always been committed to sustainable textile production since many years but its substantial contribution started when it introduced the Pulsar technology to the market in 2014. Pulsar is a revolutionary system for dyeing of yarn and tops and required approximately four years of intense research and development before it was ready for large-scale production.
Thanks to its worldwide patented circulation system, which is truly innovative in this field, Pulsar can achieve an extraordinary reduction of utility consumption such as 60% less electric energy, 30% less water and nearly 20% less steam. There about 200 Pulsar machines installed worldwide at the moment, contributing to a significant cut in CO2 emissions as compared to standard machines. Further, Ferraro has achieved remarkable results that can be summarised as a reduction in overall energy consumption by 47%, a reduction in overall steam consumption by 62% and a reduction in overall air consumption by 37%. Never before has the theme of sustainability become such an integral part of our daily lives.
Automation and digitisation are increasingly becoming important. The pandemic has further accelerated the need for these solutions. How is Batliboi Group helping customers in this field?
Indeed, the trends of digitisation and automation have together changed the industry completely. Industry 4.0 has brought all the procedures and communications to a single network, making factories smart and production more efficient than before. We have partnered with Intex, a leader in digitisation and automation solutions. Intex offers holistic and fully integrated ERP software for the complete digitisation of textile processes and planning. Intex ERP has various modules like sales and dispatch, production planning and scheduling, stocks and inventory, purchasing, costing, laboratory and recipes, quality control, textile technical data, MIS, system administration as well as an open interface for financial accounting and general ledger. It also provides plant monitoring solutions.
We work with Eliar, a company that offers complete dye house automation system. It provides mechatronic weighing and dosing systems. Eliar has developed liquid and powder chemical & dyes weighing and dispensing systems, and thanks to the control devices and automation software, it has delivered projects that integrate with the fabric, yarn dyeing and garment washing machines and the entire factory, ultimately enabling full automatic control and recording of the entire dyeing process. With the central monitoring, planning and reporting software it has developed, Eliar delivers integrated systems from the processing machine level to the factory management level.
In the field of inspection and packing automation, PLM Impianti is our partner. It was one of the first companies to take up automation applied to fabric inspection, handling and roll packing. Its system is designed to reduce time, cost and processing waste from quality control to the setup phase according to the customer’s needs. There is also available automatic machinery such as roof cranes or special robots that manage the materials in relation to the loading carriers, centrifuges and dryers. Milvus AGV automates in terms of plant material transport with our autonomous mobile robots.
Meanwhile, Mayer and Cie is all set to launch its knit link and customers will see online the availability of spare parts and manage remote maintenance options for machines and the bundling of production and machine data on this unique platform. Almost all our Principals have adopted Industry 4.0 digital technologies and next-generation IoT-enabled control systems along with AI capabilities. They have introduced complete production process monitoring systems via the Internet of Things (IoT), which can provide various real-time analytical reports and offer numerous functions. This is very useful for reorienting the manufacturing process and helps achieve high quality levels. Also, real-time remote support is possible. Data collected through machine operations feed knowledge and is also used for predictive maintenance and the prediction of potential breakdowns through machine learning technology.
There is now a convergence of analytics, robotics, artificial intelligence, digitisation, and IoT-enabled smart machine controls. Spinning process contamination sorter leader Loptex EXA’s remote control option enables the optimisation of settings and calibration. It provides to operators full assistance. EXA, by means of virtual sensors, features predictive maintenance analysis and online control of components. The focus is on the digitisation of all our machinery range with full integration in digital flows such as Industry 4.0, cloud technology and predictive maintenance for remote assistance. The possibility of interface with MRP and ERP systems makes them suitable for the right integration of data management.
—
Batliboi Group Companies
• Batliboi Environmental Engineering Ltd.: Headquartered at Thane, it operates in the field of air pollution control equipment and systems, hydrogen gas solutions and industrial fans.
• Batliboi Renewable Energy Solutions (P) Ltd.: Operates in the fields of wind and solar energy. The company’s headquarters is in Chennai.
• Spartan Electricals: Manufacturer of electric AC motors. Its headquarters and manufacturing facility is in Thane, Maharashtra.
• Quickmill Inc.: Wholly owned step-down subsidiary company of Batliboi Ltd., it is a leading manufacturer of large area CNC gantry and bridge milling and drilling machines and is based in Peterborough, Canada.
• Batliboi Impex Ltd.: Headquartered in Mumbai, the company offers complete solutions in logistics.
—
The Batliboi Portfolio
Batliboi represents world leaders in their respective fields offering sustainable technologies and solution for textile manufacturing. These include:
- Spinning: Saurer BD open end spinning, Loptex contamination sorter, Nitto Shoji comber accessories, Ratti twisting machines.
- Knitting: Mayer and Cie circular knitting machine, Busi socks knitting machine.
- Dyeing and Printing: Loris Bellini yarn dyeing machines, Pozzi Leopoldo heat recovery system, Kusters Calico wet processing machines, KTM Kranz soft flow dyeing machines, Eliar chemical and dyes dispensing system, Europrogetti ETP and zero liquid discharge system, Unitop CRP and MEE, Dettin hydroextractor, Fimat print colour dispensing system, Yilmak garment washing and dyeing machine, Krantz soft flow dyeing machine, Ichinose rotary screen printing machine, MS Italy digital printing, Milvus robotic automatic guided vehicles.
- Technical Textiles: Mayer and Cie braiding machine, Mageba narrow fabric complete solutions.
- Finishing: Ferraro balloon padder, slitter and compactors, Mario Crosta dry finishing range, Pentek continuous tumble dryers and print washer, PLM Impianti inspection and packaging machines, RF Systems dryer, Ilsung stenter machine, Seiren weft straightener.
- ERP Software: Intex Group