Supplying quality weaving machine spares is a matter of ethics for OM Corporation
Manufacturing and supplying quality weaving machine spare parts is a matter of ethics for OM Corporation. Despite the flood of imported weaving spares of low quality and prices in the last few years, the company has decided not to compromise with their fundamental philosophy of manufacturing spares of excellent quality.
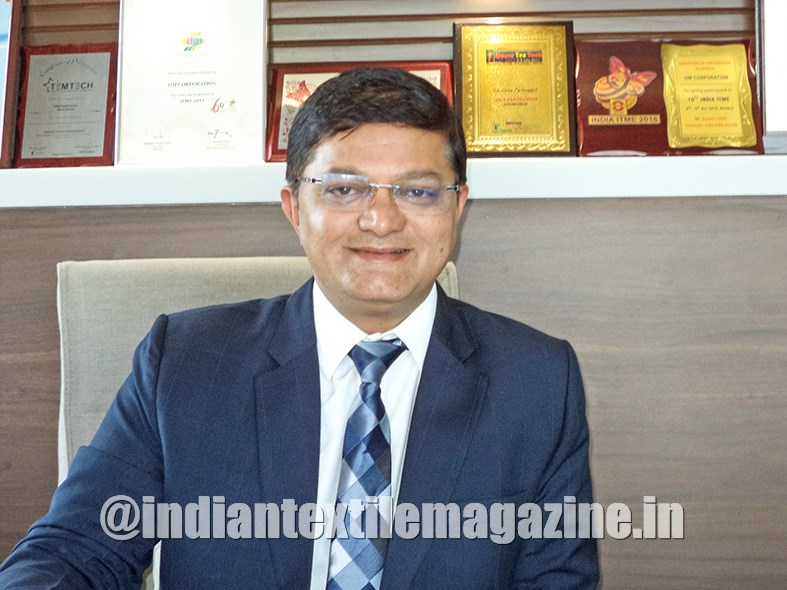
OM Corporation’s Director Bhavesh Patel believes that adhering to supplying quality spare parts will help the company survive for a long time to come.
Ahmedabad-based OM Corporation was started in 1995 and began by producing spare parts of water jet looms supplied by Tsudakoma and Nissans. At that time, only two mills – Reliance Industries and Garden Vareli – had water jet looms in India.
In the following years, Arvind Mills installed air jet looms for the first time in India, which led to OM Corporation diversifying into the production of spare parts for air jet looms.
The company uses the same metallurgy as used by the weaving machine brand, while developing a spare part for a new model and runs that spare on a trial basis for around eight months. “Only if the results are satisfying, do we take up the production of those spare parts,” Patel informs.
Elaborating about the factors that lead to good quality of the final product, Patel says that raw material is not just the prime criterion for supplying a good quality spare, as there are other factors like precision of dimension, tolerance, checking gauge, etc., must be taken into account and also claims that their quality is comparable to those supplied by OEMs.
OM Corporation manufactures spares of Tsudakoma, Picanol, Somet and Toyota air jet looms and has around 12,000 stock keeping units (SKUs), as they have to supply spares for even weaving machine models which were launched in the early 1990s as well as those introduced recently.
However, the biggest challenge that the company faces is from imports of low quality spares which are also sold at heavily discounted prices.
In the last few years, Patel has noticed a trend among smaller weaving plants moving towards using low quality spares to save on costs. But his biggest satisfaction is that the big textile mills or exporters still use good quality spares as they do not want to compromise on the quality of fabrics.
“We have stood our ground when it comes to quality and do not wish to compromise when it comes to our ethics under any circumstances. We are willing to face the onslaught of cheap imports with the confidence that the users of cheap and low-quality spares will eventually realise that it does not pay to save on spare parts costs in the long run,” Patel states.
OM Corporation currently supplies spare parts to the biggest textile mills in India such as Vardhman Group, Sangam India, Arvind Mills, Welspun, LNJ Bhilwara and many other reputed mills. The company also provides guarantee and warranty for the spares, while also undertaking to provide replacements if the problem is genuine.
Currently, it sells around 75-80% of their production in the Indian domestic market, with the rest accounted for by exports. The company exports to Bangladesh, USA, Sri Lanka, Indonesia, Turkey and Egypt, as well as a few other countries. “We are trying hard to develop and push exports by taking part in textile machinery exhibitions in various countries,” Patel says.