No two textile finishing line orders are ever the same for Monforts, which frequently develops bespoke solutions according to the specific needs of its individual customers.
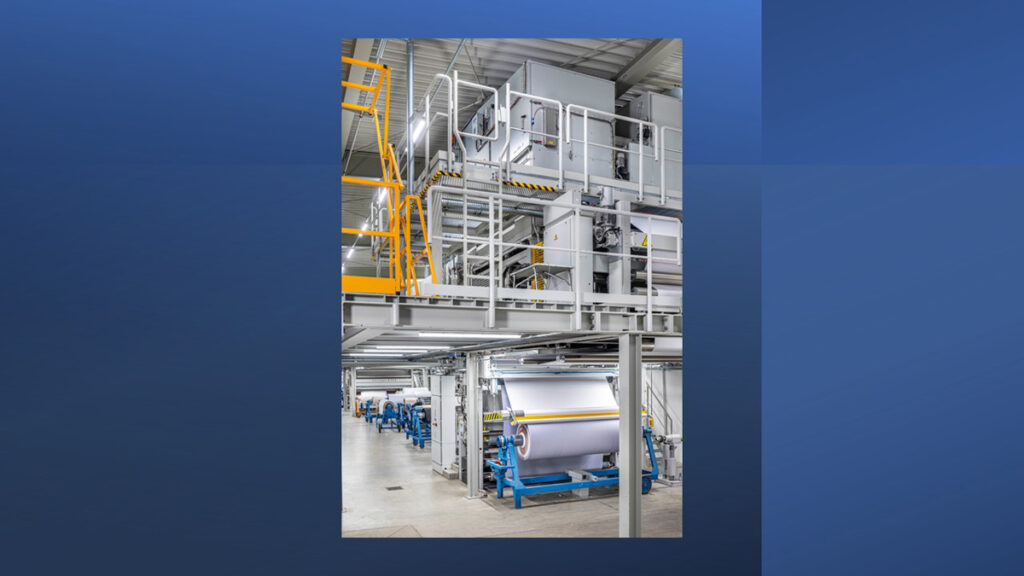
However, all of the machine builder’s resourcefulness and engineering know-how were called upon to meet the complex and unusual specifications for a recent installation of a new Montex 8500 stenter line at Curt Bauer’s plant in Aue in Germany.
Tradition
Curt Bauer has been in continuous operation for 150 years, beginning as a weaving mill in Aue in the Ore Mountains region of Saxony back in 1882. Today, with 120 employees, the company has an annual production of 2.2 million metres of fabric and specialises in three key fields – home textiles, special damask fabrics for West African garments and technical textiles.
“For bedding, the variety of patterns that can be created by jacquard machines allows very attractive designs with many subtleties to be created and there is no feeling to match sleeping on high quality damask bed linen,” says Gert Bauer, joint managing director of Curt Bauer together with his niece Claudia Bauer. “For the home textiles sector we develop themed collections allowing various individual products to be combined in high quality, contemporary styles.”
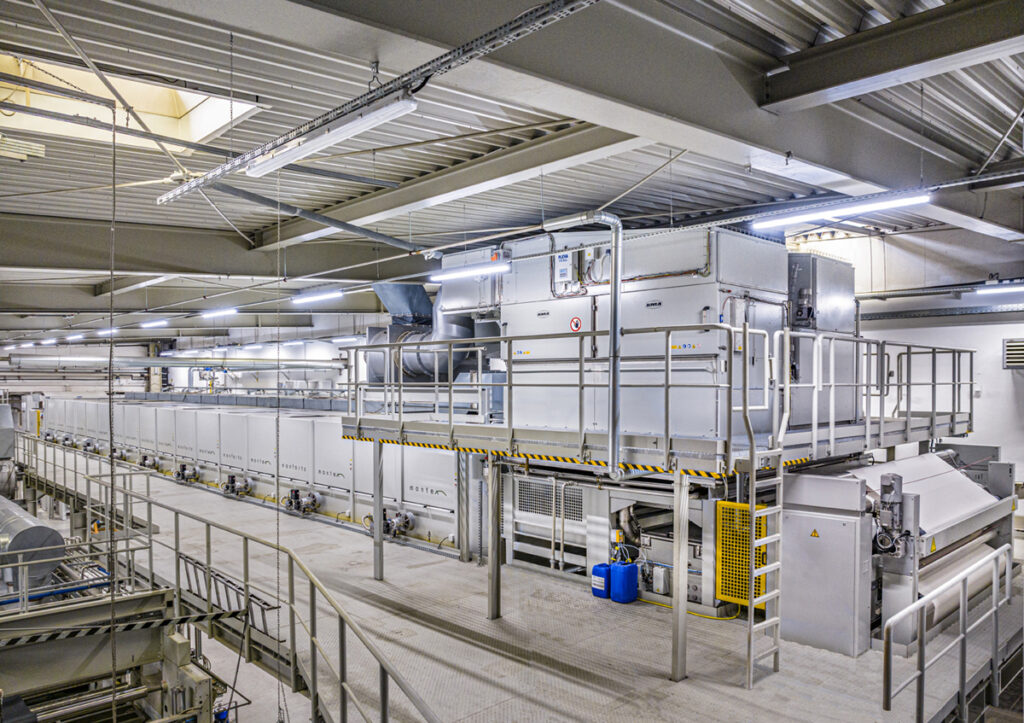
Functional fabrics
The company’s technical textiles business produces functional fabrics that can minimise or completely eliminate the need for later assembly operations, such as fabrics with woven channels into which metal struts can be inserted. These are supplied to a wide number of automotive brands for the fabric cladding of camping van roofs, or cargo cover areas in cars. Another key application is in multi-layer insulating fabrics for the roller blinds of refrigerator counters in supermarkets.
Finishing
Curt Bauer’s finishing department is primarily focused on the special damasks for West African garments and is now unique in being able to meet the requirements of this market. Singeing, bleaching, mercerizing, piece dyeing, finishing and calendering – all possible in widths of up to 3.2 metres – are all central to the success of these special wovens. In addition, the company can dye polyester and fix it before carrying out any further high-level finishing required.
A first Montex stenter was installed by Monforts at the Aue plant in 2003 and an older machine from a third party supplier was also still in operation prior to the latest upgrade.
“The replacement of our older existing stenter, which was installed in 1985, was long overdue,” explains Gert Bauer. “It had a maximum working width of 2.2 metres and we were looking to both increase productivity and reduce energy requirements.”
As a consequence, the company opted for a new Montex 8500 line with a working width of 3.2 metres equipped with the MonforClean heat recovery and exhaust air purification system. The Montex stenter remains unmatched in terms of its robustness and long service life and with MonforClean technology, the waste heat from the drying process is used to pre-heat the drying air. This results in a radical reduction in the conventional heat supply required, compared to full gas and thermal oil heating. Overall energy savings of up to 40% can now be achieved compared to conventional stenters.
Multi-level
The first challenge at the Aue plant was how to fit the significantly larger machine into the available space without restricting the area required for docking operations.
The special multi-level configuration that Monforts designers and Curt Bauer’s team devised in order to meet these requirements involved raising all of the line’s drying zones – with a combined length of over 28 metres – on scaffolding platforms, to enable the ground floor space below them to continue to be fully utilised.
The next challenge involved configuring the MonforClean system without having to make any costly changes to the roofing structure. This, Gert Bauer observes, demanded “millimetre precision”.
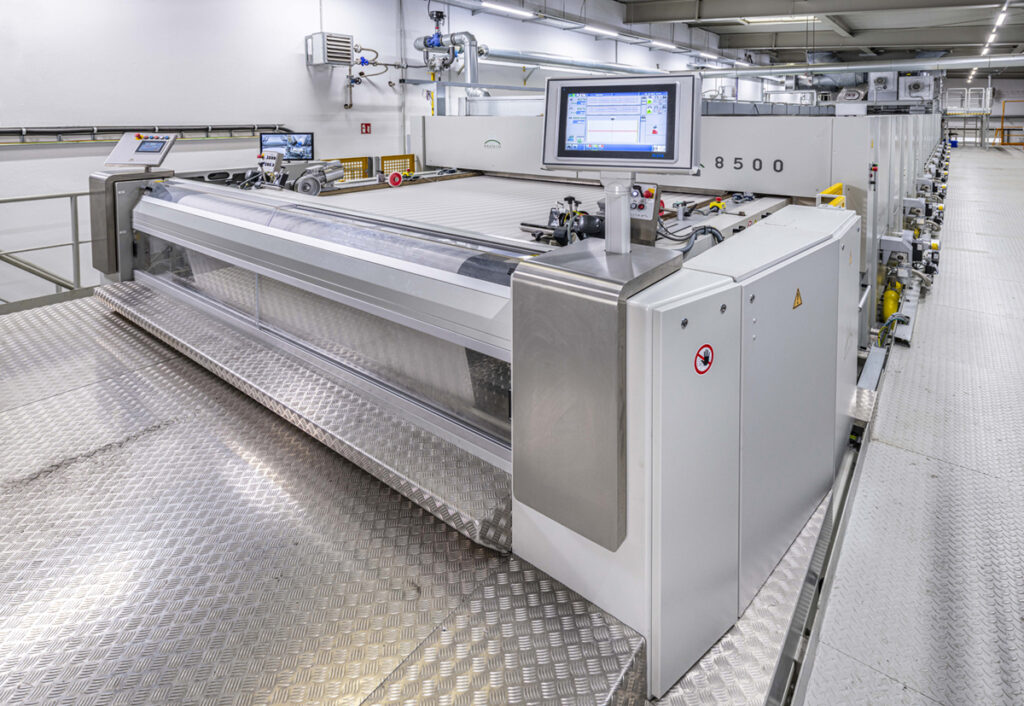
“The old stenter was dismantled and scrapped while production was ongoing, followed by the immediate installation of the foundations and the erection of the scaffolding for the dryer section,” he explains. “It was a challenging assembly operation, but we mastered it together.”
“We call the design of such customised machine layouts to fit into very confined spaces the shoehorn method,” adds Frank Breuer, technical project manager at Monforts. “It’s almost like playing Tetris.”
With the new line now fully operational, the savings it is providing have yet to be fully calculated.
“I can say that, as expected, the peak load is generally lower than both the stenter it has replaced and the Montex line we installed in 2003, especially in gas consumption,” Gert Bauer says. “The new configurations enabling better drainage of polyester fabrics through suction also help save energy. All in all, we are very satisfied with the new line and would like to thank Monforts very much for the good cooperation.”
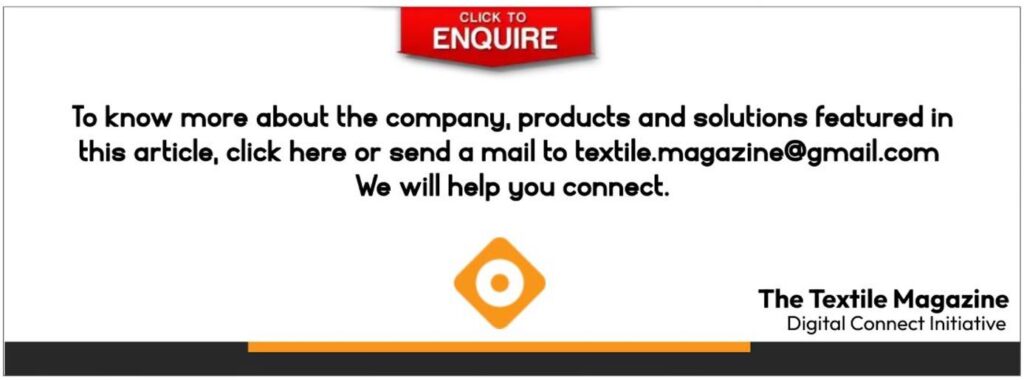