Second plant to be operational by April next
AB Carter India, a vertically integrated specialist in rings and travelers, is all set to increase its capacity by 50 per cent in the next 18 months. Its second plant will be operational by April 2016.
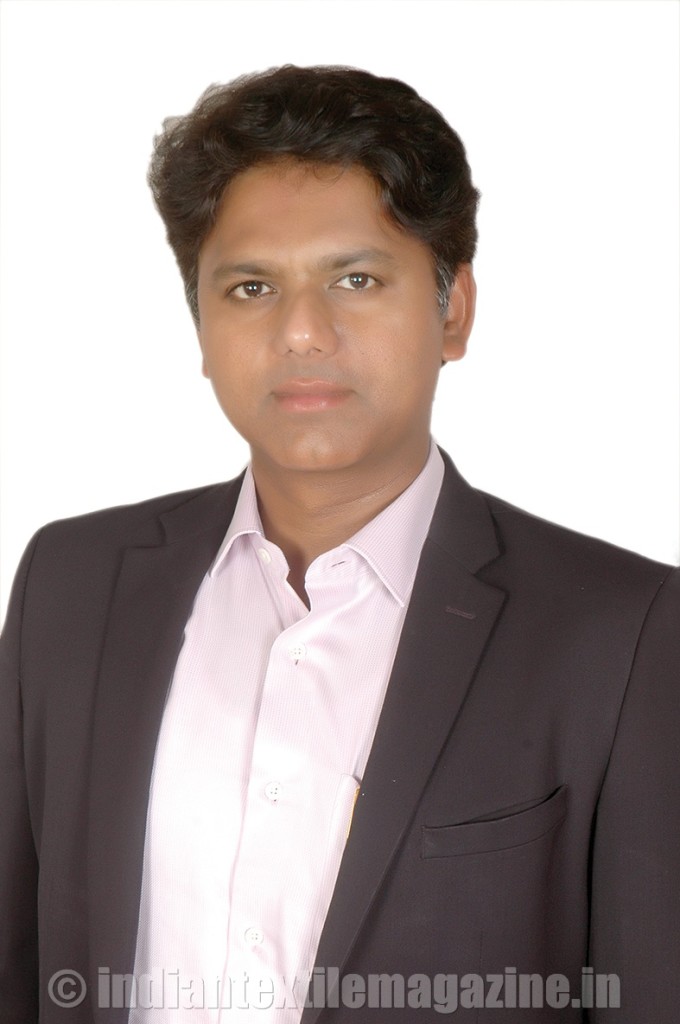
It’s all about being in the right place at the right time. At least that’s how one can describe AB Carter India, which zeroed in on India for its presence in Asia in 2006. The conviction was right because the Indian textile industry is growing at the rate of 200,000 spindles per year and is second to China globally. It’s not surprising therefore that this growth rate has prompted the company to expand its operations. A plan has been put in place whereby the existing capacity will be expanded by 50 per cent in the next 18 months.
When the global company decided to map its presence in Asia, it chose India and for the right reasons. AB Carter India Pvt. Ltd. was set up with the sole objective of addressing the pain point faced by the Indian spinner is getting world-class rings and travelers at the doorstep with 24×7 technical support.
The Textile Magazine caught up with key persons at AB Carter India who shared their experiences that have made the Indian journey so endearing.
AB Carter began its journey in Gastonia, North Carolina, in 1922. The company decided to foray into the Indian market in the 1990s through a distribution network. However, anticipating the huge future growth potential of the Indian spinning Industry, the company set up a state-of-the-art manufacturing facility on the outskirts of Bangalore in 2006. Commercial production commenced in 2008 at the plant set up at Doddaballapur, 40 km from Bangalore.
At a time when experts in the field tend to describe the textile industry as volatile, AB Carter India speaks a different language. The company has been steadily growing at the rate of 20 per cent in India over the last eight years in spite of the cyclical nature of the industry. The global centres have witnessed a 15 per cent growth. “We have targeted leading, spinning mills in India which require world-class products with effective service levels,” said Sandeep Shetty, Director, AB Carter India Pvt. Ltd.
India has been a good starting point because since the last seven-eight years the Indian textile industry has been moving towards high-speed application and yarn-friendly value-adds. It’s understandable that the spinner has had to update his product portfolio to keep pace with the requirement. “Indian spindles are about 25% higher in speed than spindles from most parts of the world,” said BR Nand Kishore, Head – Sales and Marketing.
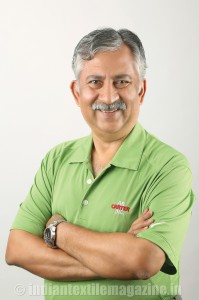
To meet the growing demand, the company has invested in capital equipment. “Before AB Carter set its base in India, the Indian spinner was forced to import world-class products at steep prices with high levels of inventory with poor levels of service,” reasoned Sandeep Shetty.
That explains how AB Carter India has positioned itself as a vertically integrated rings and travelers company. Sensing the potential of the Indian market, the company has customized its services for the domestic market, which include offerings like compact spinning and synthetic spinning. The other features include life duration enhancement, packaging options and a reduction in travel wastage.
This explains why the company has not only created a diverse range of ring travelers of different dimensions but has also enriched them with properties like low heat radiation which help in improving yarn parameters.
In terms of technology and product development, AB Carter’s recent milestones include the development of specific traveler styles for compact and high-speed spinning applications. Installation of new processing equipment to assure consistent quality and performance of travelers and rings is another highlight.
Though spinning rings and travelers are a highly competitive market with many Indian and global players fighting for a share of the market, AB Carter plans to stay ahead by ensuring that its raw material, manufacturing processes and field technical service are superior to those of competitors.
That’s how the company ranks among the top five players in the rings and travelers segment and thus entered the OEM space by taking KTTM as its client four years ago. The company is having continual technical interaction and has supplied more than 800,000 rings to KTTM. As part of the expansion plans, AB Carter India intends to strengthen its position in the OEM space by widening its portfolio.
“Overall when we look at AB Carter India, strategically the company has built its Indian business on its ability to reduce downtime. Approximately it takes about 48 hours to deliver the goods,” explained Sandeep Shetty.
Notwithstanding that, another highlight is a large portfolio with diverse applications in the traveler segment that address requirements related to spinning. Wherever required this portfolio can be tweaked in terms of yarn count, speed and application.
Many of these products with upgraded features are showcased every two to three years at international exhibitions before being formally launched in India. Of course, back-end support comes from a full-fledged R&D unit located in North Carolina which drives the innovation. The R&D Centre in Gastonia is driving innovation especially in the area of metallurgical superior raw materials and innovations in surface-technologies to improve traveler life to meet the growing demands of the spinner.
The company has been regularly ploughing back profits into R&D, be it in terms of superior metallurgical equipment, high-end testing facilities and automated processes, complete with raw materials like wires, metallurgical parts and other technicalities. This translates into the widest range of ring traveler applications – Lycra, cotton denim from the global network and expertise.
These finished products are marketed by a sales team with Indian textile background, 18 agents and eight application engineers based at strategic locations like Bhilwara, Ludhiana, Nagpur, Ahmedabad, Silvassa, Madurai, Coimbatore, Salem and Guntur.
In terms of new technologies and product launches one can look forward to new traveler styles/designs to optimize spinning performance in high-speed and compact spinning applications. The main emphasis will be on improving the traveler life in the more demanding spinning applications. “While India is a highly sophisticated market with challenging clients, we are committed to grow and service this market with quality rings and travelers,” said B.R. Nand Kishore, commenting on the Indian scenario, “Our present plant capacity is equipped to manufacture 150,000 rings and 10,000 boxes per month.”
To sum up, industry leaders in India have a vision to be the best in the world, and this market is one of the most demanding for yarn manufacturers. The production speeds are the highest in the world while still maintaining high quality standards for the yarn. India continues to invest in the latest technology to optimize productivity and quality.