Continues to partner global majors to provide end-to-end solutions
A.T.E. Enterprises Private Ltd. (A.T.E.) has been providing best manufacturing solutions to textile customers in India for 75 years now. A.T.E., with its professional approach, constantly endeavors to add latest technology products to its portfolio. The company has recently joined hands with the Savio Group, Danti Paolo and Rotondi, all from Italy, and with Texpa of Germany with the intent to provide one-stop-solution for all its customers. We speak to Mr. G.V. Aras, Director, A.T.E Enterprises Private Ltd. (TEG), on the company’s strategy and future growth plans.
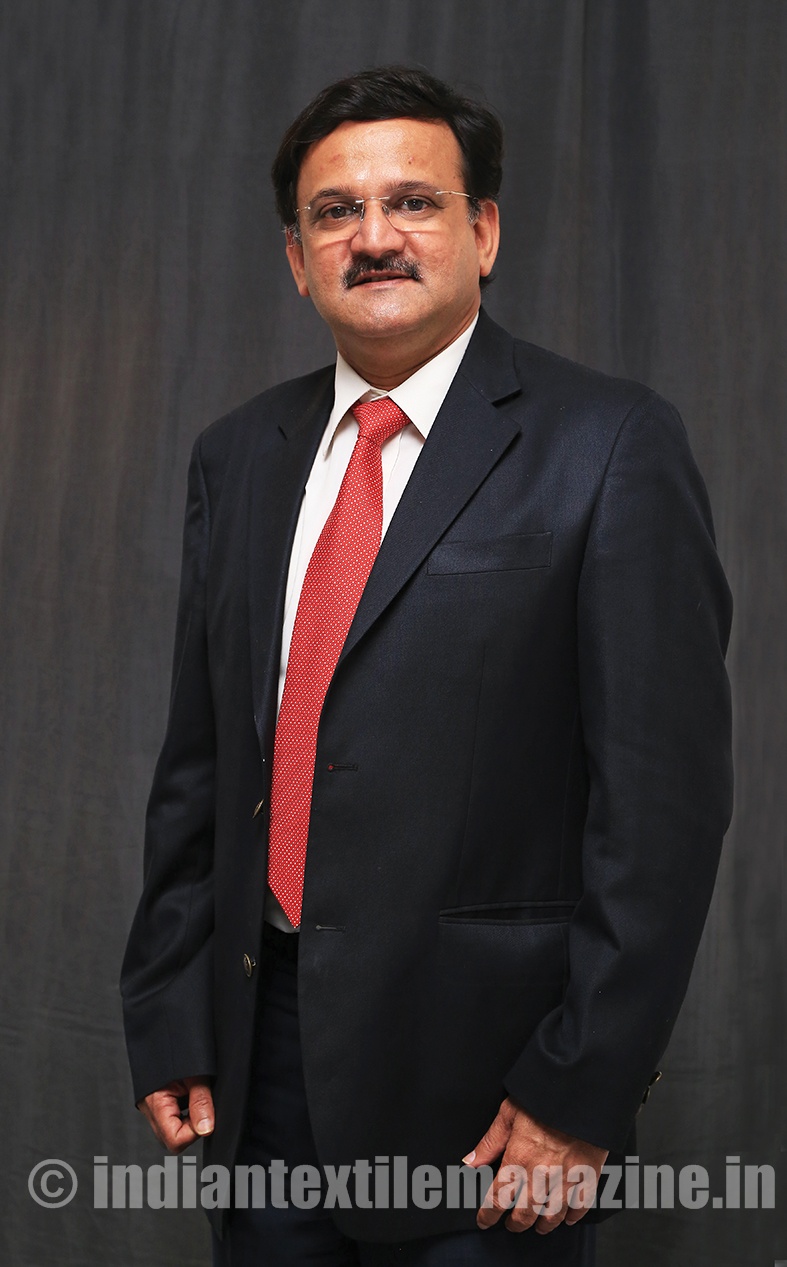
It’s been quite an interesting start for A.T.E. this year with the addition of new principals across various divisions. What is the strategy behind this aggressive approach?
At A.T.E., we have been pursuing the philosophy of ‘end to end solution’ whereby we are able to help the customers with the right technologies across the textile value chain. In that pursuit we have been always looking for filling the product gaps in our folio. Addition of Savio for automatic winding, Texpa for home textile making up and Danti Paolo for fabric finishing are the result of following the same philosophy. As a result of the ‘one window solution’ strategy, our customers also find it convenient to approach A.T.E. for their requirement. This is the only company in India from the textile machinery and accessories field that can offer the one window solution across all the segments of the textile industry which also cover utilities, effluent treatment plant and complete aftersales service solution, apart from supply of textile production machinery.
How has the year 2016-17 been for the textile industry in general? Which are the segments performing well this year?
There has been a mixed trend in the textile industry in the current year. Demand for garments and fabrics is still subdued and is likely to remain so for some more time. Due to the cotton price rise over the last two months, the spinning sector has been adversely affected. Investments in weaving are continuing, especially in high-speed air jet and rapier machines. Circular knitting is growing at very slow pace while the warp knitting industry of Surat is facing a demand crisis due to over-capacity. The processing sector is doing well and the investments are growing since last one year and good thing is that this weaker link in the value chain is now getting the required investments. Many bigger players are either modernizing their processing or adding capacities. With this, the imbalance in the textile value chain will get corrected to a large extent.
Demand for garments is yet to pick up. However investments in the garment sector are expected to increase in the coming days with the Government’s new package which encourages employment in this sector. Textile exports are also lower over the last many quarters, affecting the industry prospects. However since the monsoon has been quite satisfactory so far and expected to be so this year, the rural economy will get a boost. This, along with the implementation of the 7th Pay Commission recommendations and OROP will certainly help in boosting demand for textiles and apparels.
How has A.T.E. performed in this context?
The year 2015-16 has been one of the best years for A.T.E. Almost all the business divisions have done well. Special contribution has been from the warp knitting sector which has attracted huge investments. The processing division has also done very well with steady order inflows. We could successfully handle complete processing projects of Trident (bed linen), Morarjee (shirting & bottom weight), Himmatsingka (bed linen), Creative (bed linen) and VHM (yarn dyed shirting), nearly on a turnkey basis. The spinning division, as always, has contributed very well, in that we could increase the market share for Truetzschler blow room and cards significantly.
We did record supply of more than 830 cards of Truetzschler India to the Indian market in a single year. Since we have a strong and efficient service back-up in the machinery sector, we could strongly support our customers in aftersales service as well as technological services. In 2016-17 also we should do well as at present. With the addition of new principals like Savio in spinning and Texpa and Danti Paolo in processing we are able to cover almost all the sectors of the industry.
Coming to individual segments, Inspinning there are some major players who feel there is excess capacity in spinning in India which is making the business unprofitable for the existing players. What is your opinion on this and how is A.T.E geared up to serve the industry?
At present, apparently there is an excess capacity in spinning since a lot of new capacities has been added in the last two years, more particularly in Gujarat, due to attractive Government policies. This has certainly put pressure on the existing players due to supply surplus and subdued yarn prices. The declining yarn exports also have worsened the situation further. However over a period of next few months the imbalance on the supply side will get adjusted. Since investments are continuing in high speed weaving and knitting and further in processing, demand for quality yarn will certainly grow, thus helping in correcting the situation.
In my opinion, on an average, there will be demand for addition of 3 to 3.5 million spindles every year in spinning, half of which will be for replacement of the old capacities and the balance for addition of new capacities. If India can strengthen the garment sector and this sector becomes the growth engine of textile exports as in China, all the back-end sectors will have sustainable growth over the next many years.
With the addition of Savio in our spinning machinery portfolio we have succeeded in entering a much larger size market of automatic winders, which so far was eluding us. With the addition of Savio winders and twisters we will now be able to offer much broader and technologically advanced solution to our spinning customers since Truetzschler India also has added complete combing solution and a new high production draw frame to its manufacturing range, thus strengthening the sliver preparation side.
The weaving segment has witnessed strong growth in the last few years with many major projects being executed? Do you expect continued growth in the weaving segment? A.T.E. is representing one of the Chinese weaving machinery manufacturers. How has the response been so far for your machines?
There have been sustained investments in the weaving machinery over more than two years due to TUFS support as well as various State Government incentives. In the last couple of years, on an average 3,500 to 4,000 high speed weaving machines (from Europe and Japan) have been added. Over and above this nearly 4,500 to 5,000 medium to low-speed rapier weaving machines (from China) have been added annually. The synthetic sector from Surat has also attracted addition of nearly 3,000 waterjet weaving machines (mainly from China) annually. This growth in weaving is likely to continue since there is still quite a backlog in modernization, weaving being a weak link in the value change for the last many decades.
Since the top end of this segment is fully occupied by the leading players from Europe and Japan, there has not been much scope for A.T.E. to enter this segment. In the industry pyramid the middle and especially bottom segment is huge in size is dominated mainly by the cheaper shuttleless machinery suppliers from China. There are still more than 17 lakh powerlooms in operation in the country which cater to nearly 70 per cent of the fabric production in India. These outdated power looms certainly need gradual replacement by economical shuttleless looms. We saw a big opportunity in this situation since there is no organized player in this segment that can support customers from the start till the end in upgrading their set-ups.
With the Hangzhou Huahong low-speed rapier machines from China, which are very reliable and low in maintenance, we could offer an economically viable solution to the lower segment of the weaving market. We have been doing hand-holding for the customers from this segment supporting them with strong aftersales support due to which we are successful. Their terry towel weaving machines have been a big hit in Solapur and Ichalkaranji markets.
Knitting is another segment which is expected to witness significant growth in the coming years, thanks to the Government’s special package and encouragement for the garmenting segment. How do you expect this segment to perform?
Circular knitting offers a good value addition opportunity for spinners. There has been continuous investment in the knitting sector, both in the circular knitting machines and knit processing. While we are very strong in the knit processing sector due to our capability to offer complete solution from the world’s leading textile machinery manufacturers, we are not that much present in the circular knitting machinery segment. The Tayu brand of circular knitting machines from China had to face stiff price competition from other Chinese knitting machinery makers offering cheaper machines. However, we are very successful in selling Tayu circular knitting machines in Bangladesh, where it is one of the leading players and gets premium over other Chinese brands.
Dyeing and processing has traditionally been a strong segment for A.T.E. and we see Indian textile companies increasingly investing on high quality low solutions which cause less damage to the environment and energy efficient. A.T.E. represents the best global brands in this segment. How is A.T.E. geared up to take advantage of the emerging opportunity?
We, at A.T.E., are quite upbeat about the processing sector. This sector has long been neglected. As a result, it has remained a weaker link in the textile processes. India has never succeeded in entering the high value segment in the global textile trade mainly because of lack of good state-of-the-art processing facilities. Now this weak link is being getting corrected gradually with the addition of continuous processing capacities. This will certainly make India’s entry into high value segment easier.
A.T.E. is perhaps the strongest player in the processing machinery segment with major leading brands like Fongs, Monfongs, Monforts, Goller, Zimmer, Osthoff, Mahlo, Ramisch Guarneri, Color Service, Corino, Danti Paolo, Stalam and Texpa under its umbrella. We are the only company that can put up a complete state-of-the-art process house, including ETP, for our customers. Majority of the leading textile players are our customers while some of them, with the help of A.T.E., have installed modern processing capacities in the last couple of years which are comparable with the best in the world. In processing we have more than 40 service engineers and technologists who support the customers strongly.
In waste water (ETP) business also, A.T.E., through its unique ‘AAA’ biological solution, is emerging as a reliable solution provider. Customers also find it much convenient to discuss processing requirement with A.T.E. due to our strong domain knowledge on processes and technology. A.T.E. is a clear market leader in the processing segment in India.
Garmenting as mentioned above is slated for big growth in the coming years, thanks to the Government policies to make India globally competitive. A.T.E. is steadily establishing presence in this segment in recent years. What are your thoughts on the garmenting business?
I believe that India’s next growth in textiles is going to come in garments. This sector has been lagging behind for many decades due to wrong Government policies. India’s strength lies in textiles and made-ups, but in future it will shift to garments due to government’s clear focus on this sector in view of its export and employment potential. The recent announcement of the Rs. 6,000-crore package by the Government mainly focuses on attracting investments in the garment sector. With the expected change in the labour laws more investments will be in the labour-intensive garment sector. The global garment business so far has been dominated by countries like China, Vietnam and Bangladesh. India is expected to catch up soon in this backdrop.
With the emerging potential of the garment sector, A.T.E. decided to enter the segment and completed the value chain in the offering. Today we represent many leading brands like Juki (Japan) for stitching, Morgan (Italy) for cutting room solutions, Rotondi (Italy) for ironing solutions and Yilmak (Turkey) for garment washing and finishing. Although we made a late entry into this segment about four years back, we are confident that within the next few years our garment division will also become a leading player in this segment like our other divisions. Our textile customers are happy to work with us in the garment segment as they feel secure in dealing with one supplier offering a larger part of the technical solution.
Lastly the technical textile segment which again holds a lot of promise but investments have not matched expectations. How do you see the story on Indian technical textiles unfolding and what are the solutions A.T.E. can offer for this segment?
A.T.E. offers complete end-to-end solution in technical textiles. Perhaps it is the only company that offers technology solutions in all the segments of technical textiles, may it be woven, knitted, warp knits and non-woven or coating and lamination. We represent leading suppliers like Karl Mayer, Truetzschler nonwovens, Monforts, Zimmer and Ramisch Guarneri in this segment. Many of the leading technical textile players in the country are our customers. So far, in contrast to the hype, the investment in this sector has been low. However with the Government’s policy emphasis on investment in infrastructure and defence sectors, the technical textile segment will attract the required investments for creating new capacities.
A.T.E. also has its stake in manufacturing through a few joint ventures and partnerships. The more recent venture into manufacturing has been TeraSpin spinning components. How is TeraSpin shaping up in the Indian and global markets, and what are the company’s future growth plans?
TeraSpin has been formed after taking over the SKF spinning components business. This was done with an objective of offering world-class spinning components to the global customers. We have improvised the design and technology of SKF after the takeover due to which TeraSpin has been established as a reliable supplier in drafting, top rollers & other drafting components and spindles. TeraSpin is also a supplier to many leading textile machinery manufacturers in the world. TeraSpin is investing in innovation and development, and in the coming years it can offer many new products which will benefit the spinning customers. We also have some more manufacturing ventures in the group which also cater to the textile sector like A.T.E. Envirotech for ETP solutions, EcoAxis for remote monitoring of plants, Valence for anti-static solutions and HMX for comfort conditioning.
Finally, the fact that A.T.E. has been in business for more than 75 years is due to its strong customer relationships and service support that you have been extending to all your customers. How do you plan to further improve your service support aimed at lesser downtime and higher productivity?
One of the major contributors to A.T.E.’s success over the last 75 years has been its strong service support to customers. We firmly believe that by selling machines we actually enter into a business partnership with the customer and hence become responsible for giving full technical support to make him successful in his business. That is the reason why A.T.E. has more than 60 service people on its pay-roll, of which nearly 40 are in processing. We invest a lot in training them at principal’s manufacturing factories as well as on the customer site. Today our service engineers are highly respected by the customers for their depth of technical knowledge and the expertise in the machines they handle. Many of our foreign principals also use them across the globe due to their capabilities.
Apart from erection and commissioning, our service division in processing (customer support group) also offers other services like annual maintenance contract, machine audit, technological support and trouble-shooting services, etc. We will continue to focus on the strong service set-up at A.T.E. so that we can help customers in getting best out of the supplied machines. Many of our service engineers have received special testimonials from our customers as well as principals, which made us proud.
What are your views on GST and how is it going to have its impact on the textile industry?
One nation one tax is a great concept. Since the economic reforms undertaken by the NarasimhaRao Government in 1991, this has been the single most major reform which will impact the country in a major way. The current taxes in the textile industry vary from 4% to 12% based on different categories, while the unorganized sector has been given tax exemptions based on size. This situation has brought in lot of disparities. GST will now bring in a level playing field for all the players in the industry. A uniform tax rate will also result in efficient movement of goods in the supply chain, thus increasing the productivity and efficiency of the textile industry.
Since exports under GST would be zero rated, it would give a major boost to the country’s textile exports against the stiff competition at the global level. However, it is feared that the tax on readymade and branded garments will be at a higher rate than today. This will negatively impact this segment.