Article by Mahalakshmi G, Senior Manager – Product Management, ELGi
ELGi’s reciprocating compressors are highly reliable, ensuring the highest air quality, minimum downtime and lowest lifecycle costs. The article explains how
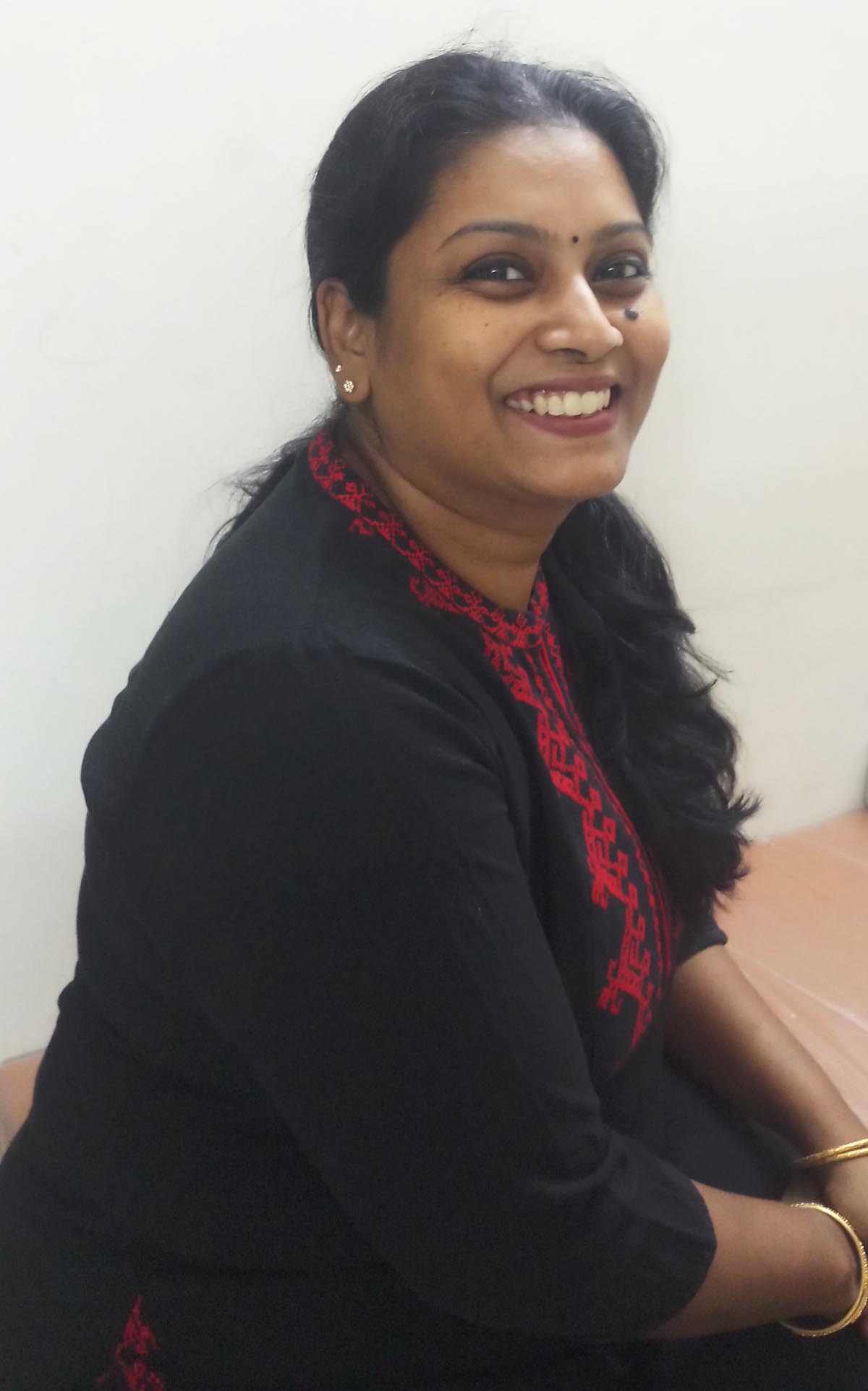
The readymade garment manufacturing industry is labour-intensive and has a fragmented supply chain. At a broader level, it starts with fibre selection, yarn, and fabric production, and then, garment manufacturing. The major operations of the readymade garment industry fall under three categories:
- Preproduction: This phase involves arranging materials, line planning, sample development and approval, sourcing, and production scheduling.
- Production: During production, fabrics are spread, cut, bundled, and sewn.
- Post-Production: Post-production includes inspection, pressing, folding, and packing, making the garment ready to sell.
The labour-dependent nature of cutting and sewing makes the readymade garment expensive. While raw materials contribute up to 50-60% of the total product cost, sewing contributes approximately 35% of the total cost. Efforts have been made to lower labour costs through supply chain management by locating production facilities in developing countries like India and Bangladesh. However, this strategy is becoming complex and difficult to sustain, forcing the industry to find alternative solutions. Thus, automating readymade garment manufacturing processes is becoming the need of the hour! Automation not only improves productivity but also the quality of the finished product by minimising human intervention and preventing errors.
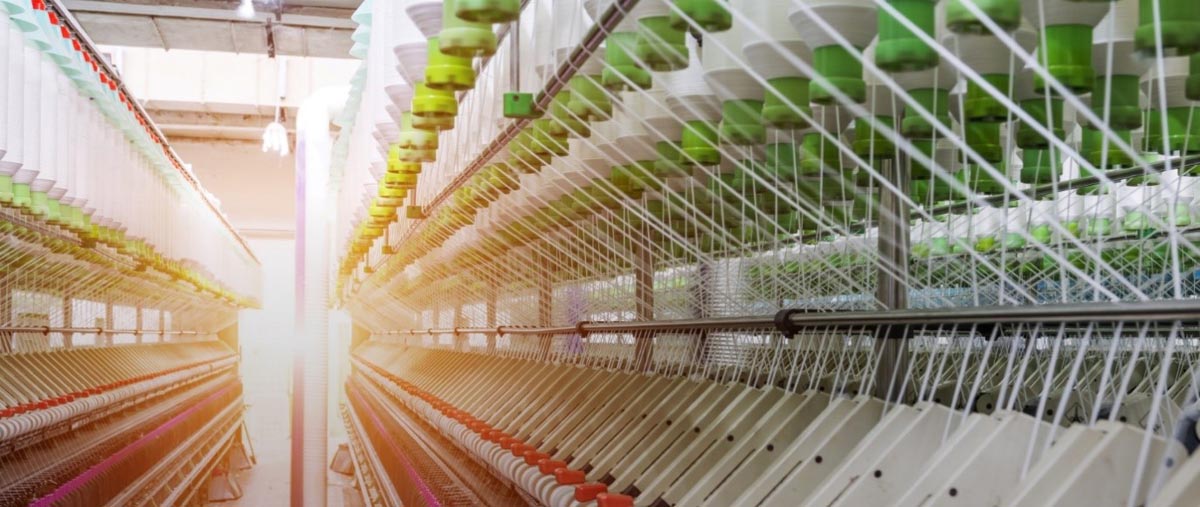
Role of Compressed Air in Sewing
Sewing is the most important process in garment manufacturing and compressed air plays a critical role in ensuring the effectiveness of automated sewing machines. Compressed air is critical for seamless sewing operations in functions like:
- The Presser Foot: It works with the feed to move fabric evenly through the machine. Air is used for lifting and lowering the presser foot for quicker action and improved productivity.
- Thread Trimmer: Excess thread must be trimmed post stitching, before proceeding to further operations. A pneumatic chain-off thread suction device cuts the thread chain and collects dust.
- Cleaning: Air is used for cleaning the stitching points at regular intervals to remove lint and dust from building up in the oil ports which form the lubrication system for the needle and presser foot.
- Needle Cooling: Needle cooling with compressed air eliminates machine stoppage, thereby increasing productivity.
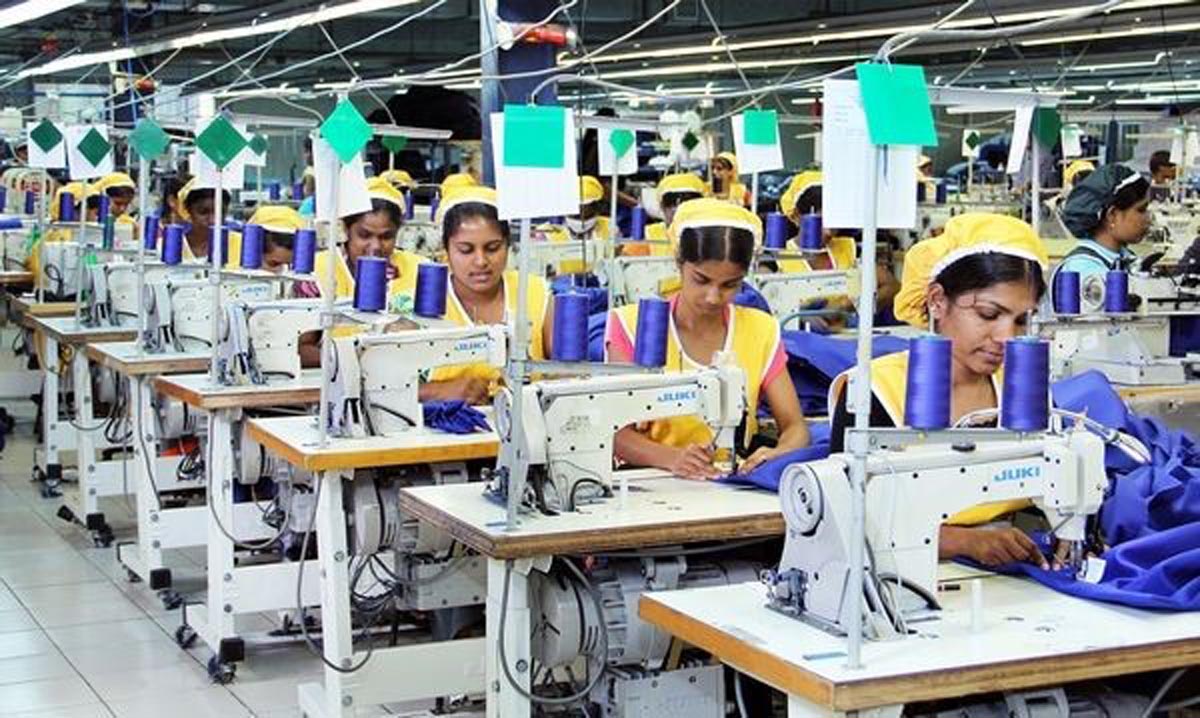
Importance of Compressed Air in Sewing Unit
The stitching industry is moving towards three important aspects – quality, productivity and energy efficiency. It is imperative to invest in the right compressed air system as the quality of compressed air directly affects the end product. The higher temperature of compressed air leads to slipped and staggered stitches. The presence of moisture in compressed air causes corrosion over a period, leaving the stitching unit with no choice but to replace the entire system. Contaminated compressed air causes oil stains to mix with the fabric and thread, leading to oil patches in the product and lint deposits in the needle.
In the absence of compressed air, the machine must be stopped at regular intervals to cool the stitching point and excess thread must be trimmed manually, costing 40-50% additional time for each piece of clothing. Productivity can be increased considerably with the aid of compressed air. Stitching units have started looking at energy efficiency as one of the key parameters during machine procurement. For smaller stitching units using piston compressors, the energy consumed accounts for at least 30% of the total electricity cost. ELGi’s reciprocating compressors are highly reliable; ensuring the highest air quality, minimum downtime, and lowest lifecycle costs. With ELGi’s two-stage reciprocating compressor, a sewing unit operating 25 sewing machines can easily save up to 9% of their annual energy cost.
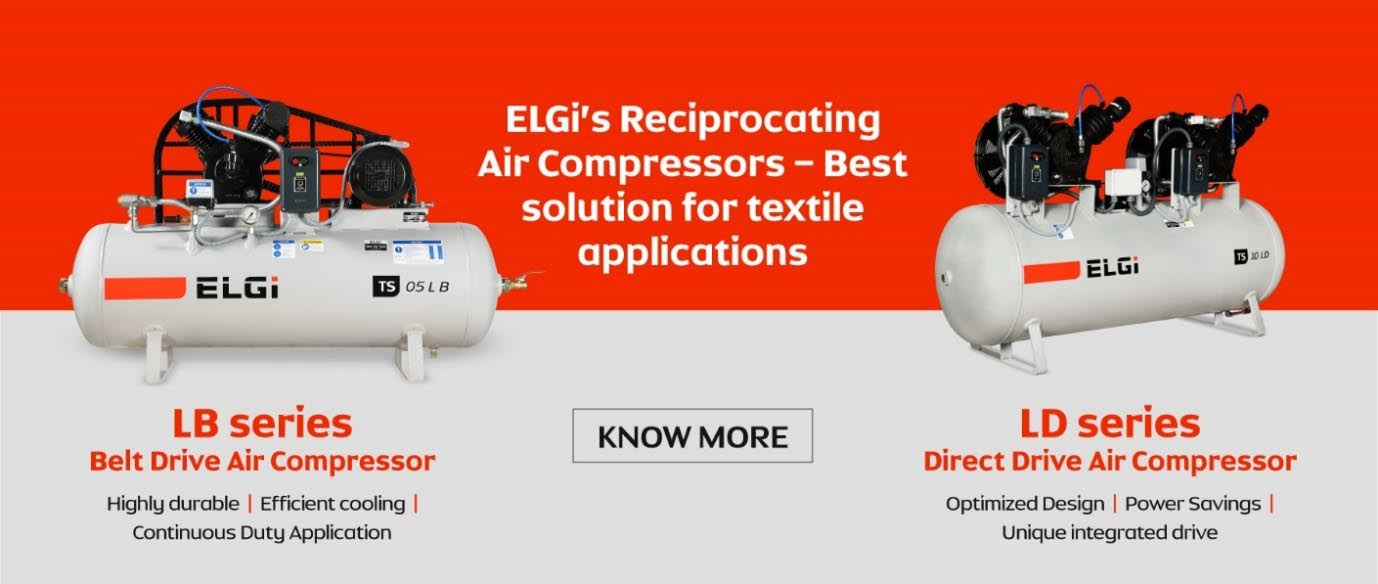
A leading textile customer in Tiruppur uses ELGi’s reciprocating air compressors in their cutting, sewing, embroidery, and printing division. They claim that their production is now “seamless and without any niggles” and that they can differentiate ELGi’s product quality compared to the compressor that they were using earlier. They consider ELGi as a “partner” offering not only a reliable product but also excellent after-sales support. By investing in the right brand and type of compressor to meet air demand and air quality, coupled with proper downstream equipment and FRL units, readymade garment manufacturers can eliminate the root causes affecting the quality of the garment, improve productivity and maximise revenue and return on investment by saving considerable energy cost.