Wear-resistant functional components, prototypes and replacement parts configured easily and delivered quickly
120,000 additively manufactured components were delivered by igus last year. Reason enough for the motion plastics specialist to further increase its capacities and equip its 3D printing service with new functions such as wall thickness and undercut analysis. In this way, customers worldwide can obtain their lubrication-free and low-maintenance components very easily and quickly, thereby saving costs.

For globally positioned companies with development teams in different countries, logistical challenges in the rapid procurement of identical additively manufactured parts are very frequent. With the igus 3D printing service, which is quickly available around the world, engineers can order, test and use the same lubrication-free and maintenance-free parts across borders – without long delivery processes. This is because igus has further increased its 3D printing capacities with two additional laser sintering printers in the USA and a further plant in China, and now delivers prototypes, small series and special parts even faster. Two further laser sintering printers are also planned for the main location in Cologne. The printed components are delivered regionally in only a few days. The cost advantages are obvious: machine downtime is reduced through the quick delivery of spare parts, development costs are saved through faster functional prototypes and delivery costs are reduced through local production.
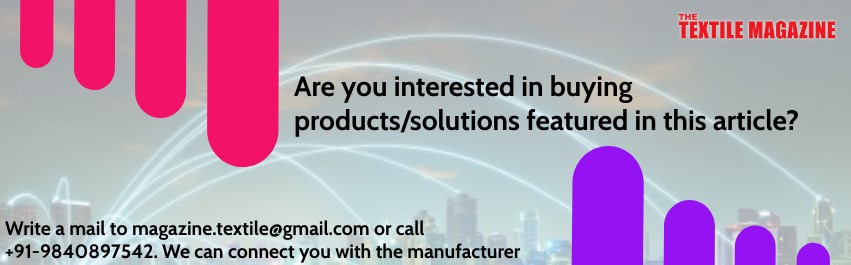
3D printing service 2.0
Ordering parts is easy thanks to the 3D printing service. First the 3D model is created and exported in STEP/STP format. The data is then dragged and dropped into the browser window. In the last step, the user can select the number of pieces and material and order or send an enquiry directly online. The new version of the 3D printing service tool now also offers the possibility to immediately check the feasibility of 3D models online. For example, the minimum wall thicknesses and the size are checked with regard to printing format capacity. In the case of print2mold (injection-moulded parts made of additively manufactured moulds), the tool also carries out an undercut analysis. After individual ambient parameters have been entered, the online 3D printing services indicates the most suitable iglidur material. Vibratory grinding and black colouring of laser sintering parts can now also be selected with a mouse click. The user gets prices and delivery times right away so that the component can be ordered or an enquiry submitted immediately.